Conveyors are the backbone of many warehouses, distribution centres, and manufacturing facilities. A well-maintained conveyor system ensures smooth operations, reduces downtime, and extends equipment lifespan. However, common maintenance mistakes can lead to costly repairs and disruptions. Here are five common conveyor maintenance mistakes and how to fix them.
- Ignoring preventative maintenance
The mistake: Many businesses only address conveyor issues when a failure occurs, leading to unexpected breakdowns and unplanned downtime.
The fix: Implement a structured preventative maintenance schedule, including routine inspections, belt tracking checks, and component lubrication. Regularly scheduled maintenance helps identify and resolve potential issues before they become major failures.
- Using the wrong or worn-out parts
The mistake: Replacing worn-out components with incorrect or substandard parts can compromise the efficiency and safety of the conveyor system.
The fix: Always use manufacturer-recommended or high-quality replacement parts to ensure compatibility and reliability. Partnering with a trusted automation and conveyor service provider, like CSL Automation, ensures you get the right parts and professional installation.
- Neglecting belt tracking and tensioning
The mistake: Misaligned or improperly tensioned conveyor belts can cause uneven wear, reduce efficiency, and lead to premature failure.
The fix: Conduct regular belt tracking checks to ensure proper alignment. Adjust tension as needed to prevent excessive strain on the system, consult a specialist to avoid further damage and operational disruptions.

- Failing to clean and lubricate components
Â
The mistake: Dirt, dust, and debris accumulation can lead to friction, increased wear, and overheating of key conveyor components.
The fix: Implement a routine cleaning and lubrication program. Use manufacturer-recommended lubricants and ensure that bearings, rollers, and chains remain free of debris. Keeping the system clean reduces unnecessary strain on components and improves efficiency.
- Overloading the conveyor system
Â
The mistake: Exceeding the conveyor’s weight capacity can cause excessive strain on motors, belts, and rollers, leading to premature failures.
The fix: Adhere to the manufacturer’s load capacity recommendations. If increased throughput is necessary, consider upgrading the system or consulting with experts to assess the conveyor’s capability. CSL Automation can evaluate your setup and recommend the best solutions for optimised performance.
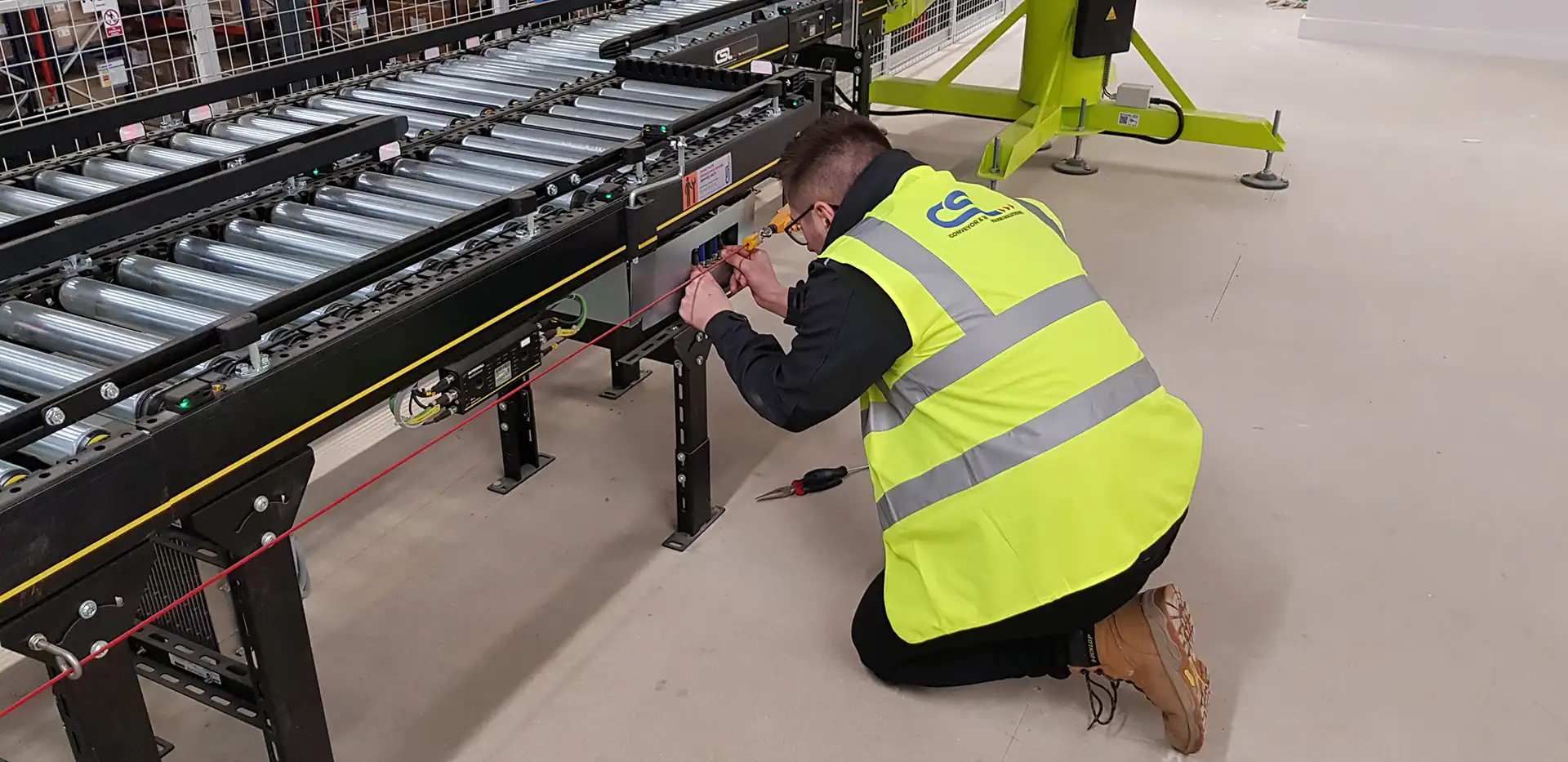
Conclusion
Proper conveyor maintenance is essential for keeping operations running smoothly and avoiding costly downtime. By addressing these common mistakes, businesses can improve efficiency, extend equipment lifespan, and reduce repair costs.
At CSL Automation, we specialise in maintaining, repairing, and upgrading conveyor systems—whether we originally installed them or not. Contact us today at [email protected] or 01283 55 22 55 to ensure your conveyor system remains in peak condition.