At CSL Automation, we understand the critical role your automation and conveyor systems play in keeping your operations running smoothly. Downtime is costly—not only in lost productivity but also in the knock-on effect it has on customer service and operational flow. That’s why proactive maintenance and future-proofing are central to our ConveyorCare service offering, with the Obsolescence Audit playing a key role.
What is an obsolescence audit?
An Obsolescence Audit is a detailed review of the critical components within your automated system—such as controls, drives, sensors, motors, and software platforms—to identify items that are approaching or have already reached obsolescence. Our goal is to help you understand the current and future risks associated with ageing hardware or unsupported technology and provide a clear path to mitigate those risks.
Why it matters
Manufacturers of automation components regularly update, replace, or discontinue older products. Without an up-to-date picture of the state of your system, you might be unknowingly relying on hardware that’s no longer available or software that’s no longer supported.
When a component fails and a replacement is no longer in production, you’re faced with:
- Extended downtime while sourcing alternatives
- The need for rushed engineering changes
- Unexpected capital expenditure
A ConveyorCare Obsolescence Audit helps you avoid these reactive scenarios by giving you control and foresight.

What’s included in the audit?
Our experienced ConveyorCare engineers carry out an on-site survey to assess:
- Age and support status of key components
- Availability of spare parts and support
- Software versioning and compatibility
- Lifecycle status from OEMs and suppliers
We then provide a comprehensive report detailing:
- At-risk components
- Recommendations for replacements, upgrades, or spares
- A tailored action plan prioritised by criticality and business impact
The benefits to your business
- Improved reliability: Reduce the risk of unexpected system failures.
- Cost control: Spread upgrade costs over time rather than dealing with emergency replacements.
- Informed investment: Plan future upgrades or refurbishments with clarity.
- Peace of mind: Confidence that your system is being proactively managed.
Independent of original supplier
Whether your system was installed by CSL or another provider, our ConveyorCare team has the experience and tools to carry out a thorough audit. We support a wide range of OEM equipment and have strong relationships with major component suppliers, allowing us to source accurate lifecycle data and recommend appropriate modern alternatives.
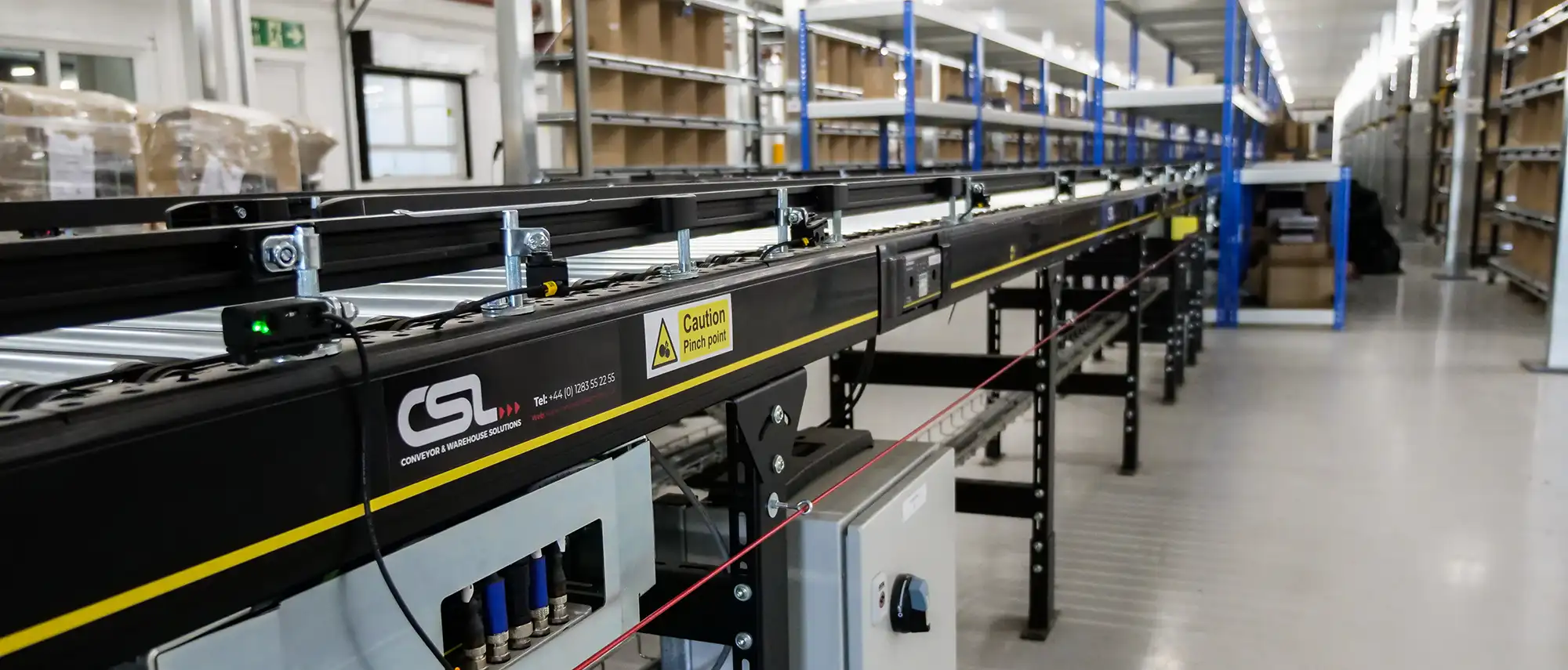
Take control of your system’s future
If you’re operating an ageing conveyor or automation system—or simply want to stay ahead of potential issues—speak to our ConveyorCare team today to arrange an Obsolescence Audit.
Call us on 01283 55 22 55
Email: [email protected]
www.cslautomation.co.uk
Let’s keep things moving.