
Automated Transportation for Products and Materials
With over 28 years experience, we pride ourselves on delivering successful installations for leading organisations. Our commitment to excellence fosters strong relationships, allowing us to provide tailored automation solutions and ongoing support.
For more information, contact us at 01283 55 22 55.
Our Clients
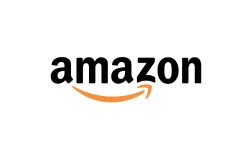










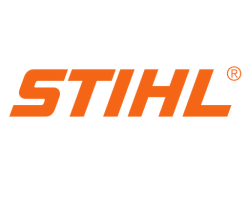
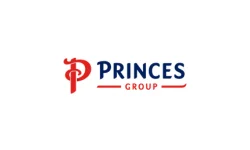





Products and Material Transit
Conveyors and automation is the link between different departments and functions within warehouses, fulfilment centres and factories.
It is often used to connect activities such as order picking to packing or inbound replenishment to storage locations.

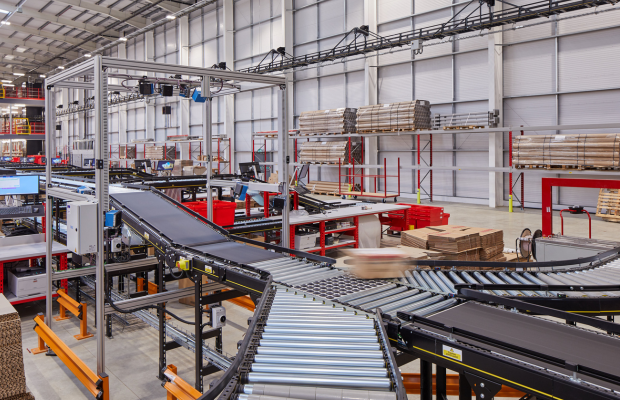
Material Transit Solutions
CSL will design the solution to suit your products, requirements, building and budget utilising technologies such as:
- Lineshaft roller conveyor
- Motorised roller conveyor (Zero line pressure conveyor)
- Belt Conveyor
- Slat conveyor
- Mattop conveyor
- AMR (Autonomous Mobile Robot)
- Pallet conveyors
automating the movement
By automating the movement of goods within a facility companies will see reductions in labour costs and MHE movements while also keeping a consistent flow.
Product transit conveyors can be used alongside other interfloor solutions such as spiral conveyors and vertical elevators.

Frequently Asked Questions
What is an automated transport system?
An automated transport system is any level of automation that can be implemented to transport items from one place to another within a warehouse. This can be achieved through utilising technology such as Autonomous Mobile Robots (AMRs), Automated Guided Vehicles (AGVs) or conveyor belt transportation.
What is the purpose of AGV?
Automated Guided Vehicles (AGVs) transport items without the need for human intervention. This automates the material handling process, allowing for a more efficient workflow, improved safety, and increased productivity.
What is the difference between AGVs and conveyors?
Transport conveyor systems have predetermined routes that are fixed and cannot be changed without redesigning the whole system. Automated Guided Vehicles (AGVs), however, do not follow a fixed path and can be redirected or take detours, displaying its flexibility. Additionally, if there are any obstructions in the AGV’s path, it can use its sensors to detect the issue and either reroute itself or wait for the obstruction to be moved to carry on its predetermined path.
More Information
Enhancing material and product movement with conveyor systems and automation
In the dynamic landscape of eCommerce, third-party logistics (3PL), warehousing, and manufacturing, optimising the movement of materials and products is essential for operational efficiency and competitiveness. Using conveyor systems and automation technologies gives you a perfect solution, revolutionising how businesses manage material flow and product handling across various industries.
Streamlined material handling & order fulfilment
Conveyor systems play a pivotal role in streamlining material handling processes within eCommerce, 3PL, warehousing, and manufacturing facilities. From receiving raw materials to transporting finished products, conveyors facilitate seamless movement throughout the supply chain.
Order fulfilment is another area where conveyor systems and automation can play a vital role in improving throughput as we as accuracy and operator safety.
By streamlining material flow, optimising order fulfilment processes, and enhancing operational efficiency, these technologies empower businesses to meet the evolving demands of today’s market while achieving higher productivity, cost savings, and customer satisfaction.
Conveyor Belt Transportation
Various types of conveyors can be used in an automated transport system. From roller conveyors to belt conveyors and chain conveyors, each type of conveyor system is designed for a specific type of product or package. For example, lighter loads don’t require conveyor systems that are heavy-duty, meaning most types of conveyor systems are ideal for these products. However, for heavier loads, a specific pallet conveyor may be better suited.
Pallet Conveyors specialise in transporting pallets weighing up to 2 tonnes, which is perfect for heavy loads. With either curves or turning tables to redirect pallets, these conveyor transport systems are ideal for the continuous transportation of goods no matter where you need them in your warehouse.
Benefits of a Conveyor Transport System
- Increased Throughput
- Enhanced Efficiency
- Improved Accuracy and Consistency
- Reduced Manual Handling
AMRs and AGVs in an Automated Transport System
AMRs and AGVs are a form of transport that can effectively carry products to wherever you require them.
AMRs are the most flexible option as they only require a few pieces of information: point of origin, destination and a map of the warehouse or area they must travel through.
With these pieces of information, AMRs can determine their own route, taking the most efficient path to increase productivity. Additionally, AMRs can detect any obstacles that may be in their path and redirect themselves, if necessary, without the need for human intervention.
AGVs differ as they require a little more information. Although they are not fixed to a specific route, AGVs still work with a guidance system. This means they follow predetermined routes but can be programmed to take detours and redirections if needed. If an obstacle is in an AGV’s way, the AGV will simply wait for the obstacle to be removed before continuing on its journey.
AGVs may need some human assistance when compared to AMRs. However, this level of automation can still have benefits, such as the capability to handle heavier loads, lower initial investment and simple maintenance.
Benefits of AMRs and AGVs
- Increased Flexibility
- Improved Safety
- Real-Time Monitoring and Control
- Enhanced Productivity
Factors to Consider Before Installing an Automated Transportation Management System
Before you invest in an automated transportation system, there are some factors you must consider to find the ideal automated transport system for your business. For example:
- The type of products you need to transport
- Operational requirements such as the level of throughput
- Flexibility and scalability
- Integration with any existing systems