
The CSL Process
Following Guidelines
Conveyor Systems Ltd follows ISO 9001:2015 quality management processes to ensure that every project, no matter the size, meets the highest standards of quality. This commitment to robust quality management ensures that each project is executed flawlessly, with a focus on customer satisfaction and continuous improvement.
Project Engagement

Your exact requirements must be considered from the first meeting to project completion. To ensure this, we will guide and advise you through every stage of the project process:
- At the initial stage, all aspects of your requirements (such as products, requirements, throughputs, ROI duration, building size, space constraints, fire exits, personnel and truck access routes, integration with existing equipment, manning levels, etc.) are considered.
- We plan and design our systems specifically to suit your product, from individual cartons or packages up to fully loaded pallets.
- Our final design is not an off-the-shelf solution but an amalgamation of standard and custom elements to ensure the perfect solution for your business.
Quotation and 3D Visualisation
At the initial quotation stage, we use 2D and 3D visualisation software to help us to develop and design the best solution to suit your requirements:
- We actively encourage regular client dialogue to help ascertain all the information required to enable us to put forward a meaningful concept and quote.
- 3D real-time simulations can be produced to prove throughputs and design philosophies.
- Accurate costings can be quickly and easily compiled, thus reducing the turnaround time.
- A detailed quotation will be presented to incorporate a comprehensive specification for all the mechanical and electrical components specific to the project.

Contract Placement & Design

Once the contract has been placed a Project Manager is assigned to your project, providing you with a single point of contact. This ensures a clear and defined line of communication from design finalisation through to commissioning:
- Our project manager and engineers complete a site survey to check all building dimensions, machinery positions, walkways, exits, etc.
- A detailed project plan defines all critical paths, installation activities, and completion dates.
- User Requirements (URS) and Functional Design Requirements (FDS) are drawn up prior to implementation based on agreed-upon technical specifications.
- Detailed project drawings are presented for your approval before the commencement of manufacture.
- Electrical and mechanical specifications can be agreed upon if you have your preferred suppliers.
System Manufacture
Besides providing a functional scheme, our priority is to design a reliable, user-friendly system which is optimised for easy maintenance and operational safety:
- Engineering layout drawings are produced using the latest design technology, which clarifies the mechanical and electrical interfacing between new and existing equipment.
- A technical liaison with other equipment suppliers is established during this phase regarding interfacing with our system.
- Offline Software and system philosophy will be tested to ensure that time on-site during commissioning is minimal.

Installation & Commissioning

Your allocated Project Manager will ensure that every aspect of delivery and installation is undertaken on time and with the minimum of disruption:
- Industry-standard as well as onsite health & safety regulations and conditions observed
- Installations are continuously monitored by the Site Supervisor and Project Manager.
- Our fully qualified mechanical and electrical engineers have extensive experience working in a wide range of industries.
- All devices are independently checked post installation, to ensure correct operation.
- Full commissioning of your system includes throughput speed testing, performance monitoring, software modifications, and diagnostics checks.
Documentation & Support
Post commissioning, we continue to provide adequate technical support and advice to guarantee optimum performance from your installation to ensure many years trouble trouble-free service.
- We include CE marking of the equipment (stand-alone or integrated), issued with your documentation.
- Comprehensive documentation (according to project type) including maintenance schedules, operational safety recommendations, itemised spares list, finalised drawings and maintenance contracts.
- Out-of-hours maintenance/breakdown service available.
- Full training is available for operators and Management to help ensure a seamless handover and implement in-house maintenance programmes.

Maintenance

Every conveyor and automation system needs regular inspections and servicing to limit breakdowns. CSL’s ConveyorCare is the answer, a combination of aftersales solutions including:
- Regular mechanical Service inspections
- Preventive maintenance schedules
- Electrical service contracts
- Spare parts
- Breakdowns
- SLA’s
Maintenance is also essential to ensure top productivity and safety, and conveyor systems are a significant investment. These systems must operate effectively with minimal downtime to get the best return.
Please find out more about our range of tailored maintenance packages with our ConveyorCare plan.
With over 28 years experience, we pride ourselves on delivering successful installations for leading organisations. Our commitment to excellence fosters strong relationships, allowing us to provide tailored automation solutions and ongoing support.
For more information, contact us at 01283 55 22 55.
Our Clients
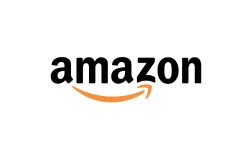









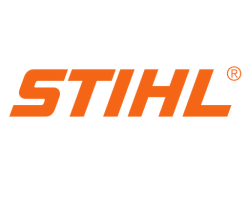
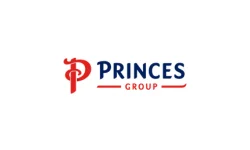





