
Automated Returns
With over 28 years of experience, Conveyor Systems Ltd delivers high-performance returns handling systems for leading eCommerce and 3PL organisations. Our tailored automation solutions help reduce operational costs, streamline returns, and build long-term success.
For more information, contact us at 01283 55 22 55.
Our Clients
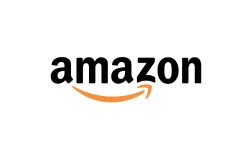









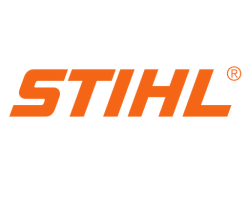
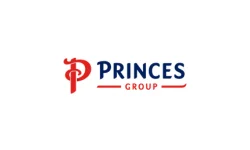





Returns handling systems
Within eCommerce and third-party logistics (3PL) organisations, managing product returns is an inevitable aspect of operations. One that, if not managed properly, can become a costly headache.
By implementing automated returns through conveyor systems, you can reap the benefits of operational efficiency, reducing the reliance on manual labour and minimising errors in handling returned items while quickly getting re-sellable products back onto the shelf.
Returns handling systems automate key stages in the returns process – reducing manual intervention, cutting costs, and accelerating the time it takes to restock re-sellable items.


automation for returns
Implementing an automated solution for your returns process can transform warehouse operations:
- Inbound items can be automatically distributed to operators
- Waste packaging moved away using trash conveyor belts
- Stock is moved back to the pick face quickly & efficiently
- Check weight to ensure returned products are intact
- Product movements linked to WMS for full visibility
- Conveyors are integrated with workstation desks
- Streamlined returns processes reduce congestion
- Faster returns improve customer experience
Minimise the Cost of Returns
No matter how your business currently manages returns, CSL can help you optimise the process. Our returns handling systems are fully customisable and can be deployed as stand-alone solutions or as part of a wider automation project.
We design, supply, and install intelligent systems that deliver lasting value and scalability for your operation.

Frequently Asked Questions
What is returns automation
Strictly speaking, automated returns processing is where technology and machinery, such as conveyor systems and robotics, are used to optimise the handling of returned items. This automation aims to streamline the entire process of returns, improving operational efficiency and minimising errors. The types of technology and machinery we use are:
- Efficient Conveyor Systems: Our high-speed conveyor systems allow for faster processing whilst taking into account the fragility of products, providing more streamlined handling. With conveyor systems, you can easily route items to designated areas where they can be further processed.
- Integration with Warehouse Management Systems (WMS): Our automated systems can be integrated with WMS to collect data on returned items. This provides vital information for your business, such as customer insights into reasons for return, which can help inform future business decisions.
- Barcode and Radio-Frequency Identification Technology (RFID): Implementing barcode or RFID technology ensures accurate tracking and identification of returned products. This prevents errors in restocking and reshipping, provides customers with a faster returns process, and increases customer satisfaction.
- Autonomous Mobile Robots (AMRs): These small but powerful robots can facilitate the movement of returned items to their specific locations in a warehouse. Using advanced navigation software, AMRs can manoeuvre themselves around a warehouse independently, allowing for a more efficient returns process.
Can the automated returns system be customised to handle specific business requirements or products?
At Conveyor Systems, our number one priority is to provide our customers with tailored solutions for their business needs. Our conveyor systems are designed with all your requirements in mind, providing you with the perfect conveyor system to suit your business. Additionally, all of our conveyor systems are modular, meaning you can also expand your conveyor system depending on the fluctuations in returns.
How automated order returns work
Implementing one or more of our automation services can easily automate the returns process. From conveyor systems to the latest technology, we can help transform your business with some simple changes.
- Item Arrival: The returned item will arrive at the warehouse, where it can be logged into the system with a barcode or RFID tag. This allows the order to be tracked through the returns process.
- Sorting: Conveyor systems and automation technology can sort returned orders based on predetermined criteria. Automated sortations can also redirect items to specific locations.
- Quality Control: There can be various reasons why an item is returned, from the product being too large to the item being damaged. Quality control will help assess the condition of the returned items.
- Data Collection: Data on returned items can be collected using an integrated Warehouse Management System (WMS). This information can provide insights into customer behaviour crucial for data analysis and business strategies.
- Routing: Based on sorting and inspection, the conveyor system will now route the returned order to a designated area in the warehouse. This area could be restocking, refurbishing, recycling, or disposal.
- Restocking, Refurbishment, or Disposal: Items deemed adequate can be sent to restocking, where they will be placed back onto the shelves ready for sale. Damaged items could be sent to various areas, such as refurbishment if the item can be repaired or disposal where the product will be recycled or disposed of.
- Customer Communication: Customers can receive notifications through automated systems. From receipts to providing updates on the processing status, implementing an automated returns process will give customers full visibility of returned items.
How do automated returns systems improve efficiency?
Automated returns systems automate sorting, validation, restocking, and waste removal, streamlining the entire returns process and reducing reliance on manual labour.
Can CSL integrate returns handling with my existing WMS?
CSL’s systems can be fully integrated with your Warehouse Management System (WMS) for improved visibility, accuracy, and real-time reporting.
Is a returns handling system suitable for small operations?
We provide scalable solutions tailored to both small and large operations. Automation can be phased in as your business grows.
How quickly can an automated returns solution be installed?
Installation times vary depending on your site and system complexity, but CSL’s experienced team ensures minimal disruption and fast project delivery.
More Information
Order returns
Within eCommerce and third-party logistics (3PL) organisations, managing product returns is an inevitable aspect of operations, one that demands meticulous attention to detail and efficiency. By implementing automated returns through conveyor systems, you can reap the benefits of operational efficiency, reducing the reliance on manual labour and minimising errors in handling returned items.
With high-speed conveyors, sorting mechanisms, and integration with advanced technologies like barcode and RFID, businesses can achieve faster and more accurate returns processing. Automation also facilitates real-time visibility into the returns pipeline, allowing for better inventory management and data-driven decision-making. Ultimately, this not only reduces operational costs but also improves customer satisfaction by accelerating the refund or exchange process, leaving customers happy with their returns experience.
What is Automated Returns Processing?
Strictly speaking, automated returns processing is where technology and machinery, such as conveyor systems and robotics, are used to optimise the handling of returned items. This automation aims to streamline the entire process of returns, improving operational efficiency and minimising errors. The types of technology and machinery we use are:
- Efficient Conveyor Systems: Our high-speed conveyor systems allow for faster processing whilst taking into account the fragility of products, providing more streamlined handling. With conveyor systems, you can easily route items to designated areas where they can be further processed.
- Integration with Warehouse Management Systems (WMS): Our automated systems can be integrated with WMS to collect data on returned items. This provides vital information for your business, such as customer insights into reasons for return, which can help inform future business decisions.
- Barcode and Radio-Frequency Identification Technology (RFID): Implementing barcode or RFID technology ensures accurate tracking and identification of returned products. This prevents errors in restocking and reshipping, provides customers with a faster returns process, and increases customer satisfaction.
- Autonomous Mobile Robots (AMRs): These small but powerful robots can facilitate the movement of returned items to their specific locations in a warehouse. Using advanced navigation software, AMRs can manoeuvre themselves around a warehouse independently, allowing for a more efficient returns process.
How Automated Order Returns Work
The process of returns can be automated easily with the implementation of one or more of our automation services. From conveyor systems to the latest technology, we can help transform your business with some simple changes.
- Item Arrival: The returned item will arrive at the warehouse, where it can be logged into the system with a barcode or RFID tag. This allows the order to be tracked through the returns process.
- Sorting: Conveyor systems and automation technology can sort returned orders based on predetermined criteria. Automated sortations can also redirect items to specific locations.
- Quality Control: There can be various reasons why an item is returned. From the product being too large to the item being damaged, quality control will help assess the condition of the returned items.
- Data Collection: Data on returned items can be collected using an integrated Warehouse Management System (WMS). This information can provide insights into customer behaviour that are crucial for data analysis and business strategies.
- Routing: Based on sorting and inspection, the conveyor system will now route the returned order to a designated area in the warehouse. This area could be restocking, refurbishing, recycling, or disposal.
- Restocking, Refurbishment or Disposal: Items deemed adequate can be sent to restocking, where they will be placed back onto the shelves ready for sale. Damaged items could be sent to various areas, such as refurbishment if the item can be mended or disposal where the product will be recycled or disposed of.
- Customer Communication: Customers can receive notifications through automated systems. From receipts to providing updates on the processing status, customers will be able to have full visibility of returned items with the implementation of an automated returns process.
Addressing the Challenge of Product Returns
Product returns pose a significant challenge for e-commerce and 3PL companies, often requiring intricate processes to inspect, restock, or refurbish items before reintroducing them back into inventory. Manual handling of returns not only prolongs processing times but also increases the likelihood of errors, impacting both operational efficiency and customer experience.
Conveyor and automation systems offer a transformative solution to streamline the returns handling process, empowering companies to navigate the complexities of reverse logistics with precision and agility. By automating key tasks and optimising workflow, these systems revolutionise how product returns are managed, offering a myriad of benefits that redefine efficiency and accuracy.
Benefits of Automated Returns
Why Choose Us to Automate Your Returns Process
Error reduction: Automation minimises the risk of human error inherent in manual returns handling processes. Barcode scanning, automated sorting, and intelligent routing mechanisms ensure accurate identification and processing of returned items, significantly reducing the likelihood of misplacements or discrepancies.
Accelerated processing times: Conveyor systems facilitate the seamless movement of returned items throughout the facility, expediting the processing and inspection stages. Automated sortation algorithms categorise items based on predefined criteria, enabling swift decision-making and efficient disposition, whether for restocking, refurbishment, or disposal.
Enhanced visibility and traceability: Integration with inventory management systems provides real-time visibility into the status and whereabouts of returned items. Automated tracking and documentation of each stage in the returns handling process ensure transparency and accountability, enabling companies to monitor performance metrics and identify areas for improvement.
Optimised resource allocation: Automation reallocates human resources from repetitive manual tasks to value-added activities, such as quality control inspections or customer service support. By automating routine processes, companies can optimize workforce utilisation and allocate skilled personnel to tasks that require critical thinking and problem-solving.
Improved customer experience: Streamlined returns processing translates to faster resolution times and refunds for customers, enhancing overall satisfaction and loyalty. Automation ensures consistency and reliability in handling returns, fostering trust and confidence in the brand’s commitment to customer service excellence.
What types of items can be processed through automated returns systems?
With new emerging technologies, our expertise has developed and expanded into automation and advanced software, changing the way warehouses work. Our knowledge and experience make us the ideal choice for upgrading your return process to an automated one.
We pride ourselves on creating customised solutions for our customers and ensuring their needs are addressed. By choosing Conveyor Systems, we can ensure you have a more efficient, reliable and accurate automated returns process, increasing not only your productivity but also your customer satisfaction.
At Conveyor Systems, we have over 25 years of experience in all aspects of conveyor systems, transforming the way businesses operate. With new emerging technologies, our expertise has developed and expanded into automation and advanced software, changing the way warehouses work. Our knowledge and experience make us the ideal choice for upgrading your return process to an automated one.
We pride ourselves on creating customised solutions for our customers and ensuring their needs are addressed. By choosing Conveyor Systems, we can ensure you have a more efficient, reliable and accurate automated returns process, increasing not only your productivity but also your customer satisfaction.