
Automated Vertical Storage
automated storage
Automated vertical storage systems are advanced goods-to-person retrieval solutions designed to maximise warehouse efficiency. By storing materials in vertically stacked trays or bins, they make use of otherwise unused vertical space, freeing up valuable floor area in your warehouse, factory, or distribution centre.
These automated storage systems retrieve items quickly and bring them to an ergonomic access point, eliminating unnecessary operator movement. With the goods-to-person principle, order picking is:
- Fast: reduced walking time means more orders fulfilled per hour.
- Accurate: 100% picking precision reduces costly errors.
- Secure: stock remains protected until released via authorised access.
Whether you need automated parts storage for small components or a large-scale automated vertical storage system for bulk goods, CSL designs and installs solutions tailored to your operation.
Benefits of Automated Storage
- Space efficiency- saving of up to 90% compared to traditional storage
- Time efficiency: reduce the need for operators to traverse vast warehouses, optimising product retrieval times.
- Safety & Security: stock can be secured and only accessed with a login
- Significant improvements in picking accuracy
- Reduce labour costs as one person can operate the machine

automated storage and retrieval system
Our automated storage and retrieval systems (AS/RS) are fully configurable to suit:
- Product type and weight
- Available floor space and ceiling height
- Required access points
- Integration with warehouse management systems (WMS)
From compact automated vertical storage units to large-scale warehouse AS/RS, CSL provides tailored solutions for e-commerce, manufacturing, engineering, and logistics businesses. Contact our solutions team to discuss your requirements.
Applications of Automated Vertical Storage
Automated storage isn’t just for large corporations, businesses of all sizes can benefit. Typical applications include:
- E-commerce fulfilment centres: high-volume order picking with fast turnaround.
- Manufacturing: secure parts storage near production lines.
- Engineering workshops: storing heavy or awkward components.
- Distribution hubs: fast sorting and retrieval for outbound orders.

Integration with Warehouse Management Systems
CSL’s vertical storage systems can be integrated directly with your WMS, ERP, or inventory control software, enabling real-time stock visibility, automated replenishment alerts, and streamlined workflows.
With over 28 years experience, we pride ourselves on delivering successful installations for leading organisations. Our commitment to excellence fosters strong relationships, allowing us to provide tailored automation solutions and ongoing support.
For more information, contact us at 01283 55 22 55.
Our Clients
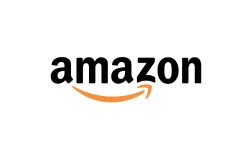









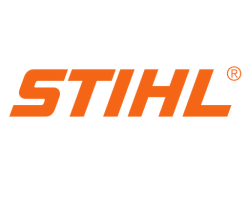
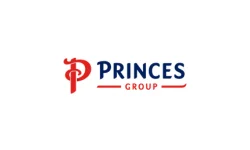






Frequently Asked Questions
How quickly can an Automated Vertical Storage System be installed?
An automated storage system is a computer-controlled solution that stores and retrieves items with minimal human intervention. It typically uses vertically stacked trays, bins, or shelving combined with automated lifts to bring the required items to an operator, improving speed, accuracy, and space efficiency.
What is the automated storage system?
With their design focused on rapid installation, most systems can be up and running in a significantly short timeframe. However, the exact duration may vary based on the model and site specifics.
How does the system improve stock management?
Automated Vertical Storage Solutions have features that consistently record and track stock levels. This ensures real-time updates and efficient stock management.
What is an example of an automated storage and retrieval system?
A common example is an automated vertical lift module (VLM). In this system, products are stored in trays that are automatically delivered to an access point at the operator’s height when requested. Other examples include horizontal carousels and pallet shuttle systems.
Can the system be integrated with other warehouse management software?
Most advanced solutions integrate with a range of warehouse management software, enhancing efficiency.
Are there any fully automated warehouses?
Many modern logistics facilities operate as fully automated warehouses, using a combination of AS/RS, robotic picking arms, autonomous mobile robots (AMRs), and conveyor systems. These facilities can manage storage, retrieval, picking, packing, and shipping without direct human handling, although operators often oversee the process.
What maintenance does an Automated Vertical Storage System require?
Regular maintenance is minimal but important for the system’s longevity. It typically includes periodic checks on the motor, software updates, and occasional cleaning.
Are the trays Configurable?
Yes, the trays can be changed by moving the internal dividers to suit the products in each tray. This can be different on each tray.
More Information
Automated Vertical Storage Systems & Solutions
Automated vertical storage systems work to optimise warehouse and distribution centre storage. These systems retrieve items from vertically stacked trays or bins, bringing them to an accessible pick-up point.
By capitalising on the full height of a facility, they reduce the floor space required for storage. All while increasing the accuracy and speed of inventory retrieval. These solutions streamline operations in an era where rapid order fulfilment is crucial. They reduce human error and maximise your storage density. Allowing you to modernise your storage approach and ensuring you stay competitive in the fast-paced logistics landscape.
Key features
Here are the key features:
- Rapid installation: Minimise operational disruptions with our quick setup, ensuring a speedier return on investment.
- Operator bays: Designed for hassle-free picking and refilling. These bays dramatically streamline the workflow and decrease manual labour.
- Motorised elevator: At the heart of our AVSS is a central motorised elevator. This ensures rapid and smooth movement of product trays for immediate inventory access.
By harnessing these features, our systems promise a seamless transition to a more efficient, space-saving, and time-optimised storage system. Letting you experience the next level in warehouse operations.
Benefits of automated vertical storage systems (AVSS)
- Space efficiency: Save up to 90% of your existing storage area.
- Time efficiency: Negate the need for operators to traverse vast warehouses, optimising product retrieval times.
- Safety & security: Elevate safety by eliminating high-level access and enhancing security, granting entry solely to authorised personnel, and ensuring stock protection.
- Precision & productivity: The integrated system identifies products, increasing accuracy in storage and retrieval processes.
- Optimal stock management: Stay ahead with consistent and automated stock-level recordings. Enabling precise inventory tracking and management.
Choosing the right storage system for your needs
Selecting the perfect automated vertical storage system requires understanding your industry’s specific demands. You should consider the volume of items stored, retrieval frequency, and any unique specs your goods may need.
These systems thrive in diverse settings, proving pivotal in industries like eCommerce with rapid order fulfilment. They are also beneficial in manufacturing, where component accessibility can drive efficiency. And also in pharmaceuticals, where precise storage and retrieval can make a marked difference. With extensive stock varieties, the retail sector also stands to gain from such systems.
A tailored solution not only satisfies your current needs but anticipates future growth and shifts in demand. Choosing wisely can revolutionise your operation, fostering scalability and enhanced performance.