Entertainment Supplier – Pick/PACK system
The client, a wholesale distributor of DVDs, Blu-Rays, and books, sought to improve order picking efficiency and streamline operations, handling various carton sizes and tote bins with fluctuating throughputs. The project required a live storage/pick system, with processes for manual inspection, order changes, and sealing before delivery to the dispatch area.
The system was designed to accommodate future expansion, including automated case sealers and tote strappers. Given the high value of the products, accuracy was critical, and the conveyor software (WCS) needed to interface with the customer’s in-house WMS.
Our Solution
A dual-function scan point captures errors and directs products to the bulk pick area. The main pick zone features 10 live pick areas, with motorized rollers and barcode readers linked to the client’s WMS. Items are diverted to ergonomic pick positions for efficient handling.
The WCS monitors order flow, and incomplete orders are recirculated. Completed orders are QA-checked, then packed and transported via an Ambaflex SpiralVeyor to a palletizing area. The Operations Manager praised CSL for delivering a reliable, efficient system that streamlined the pick/pack process and improved overall productivity.
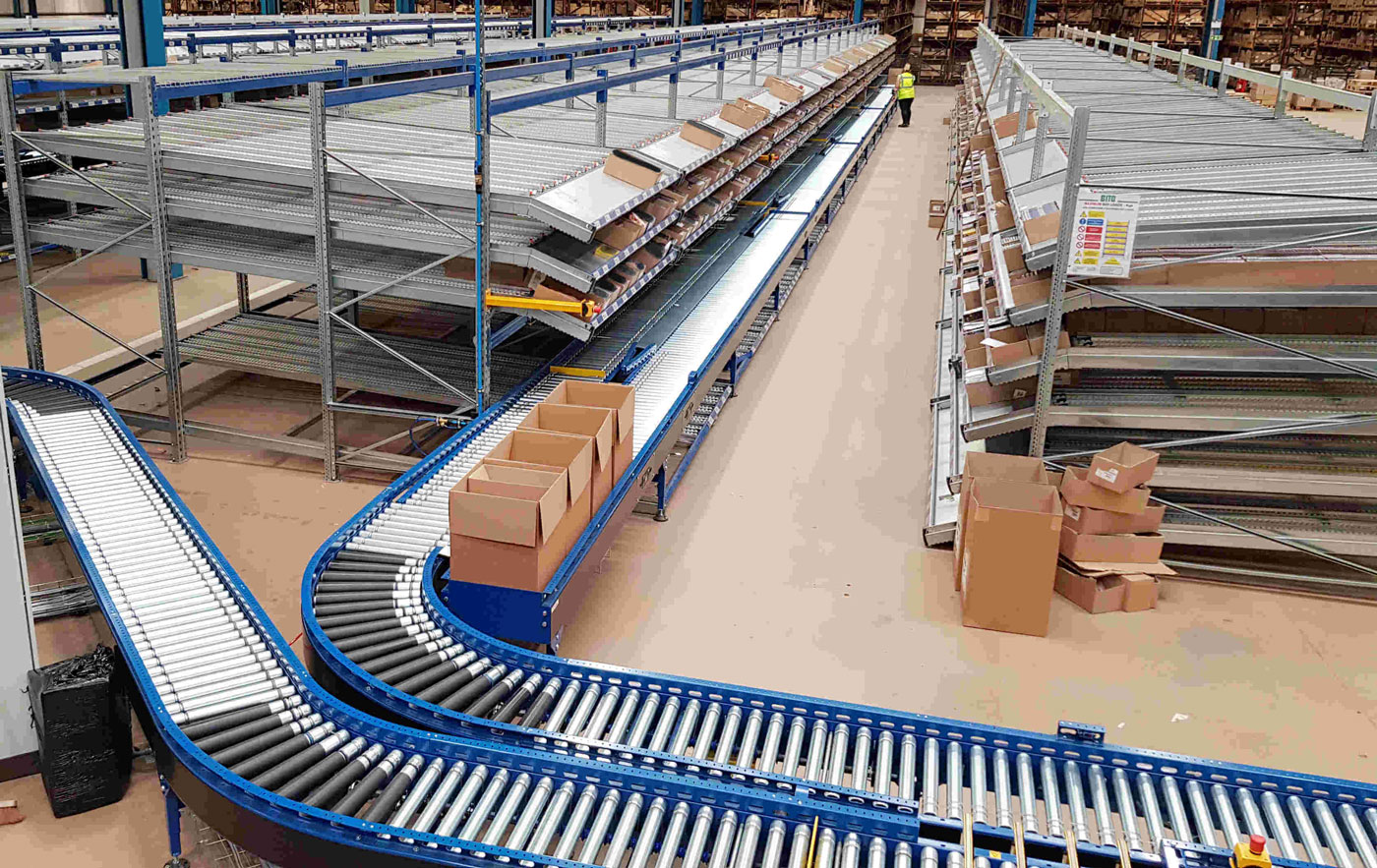