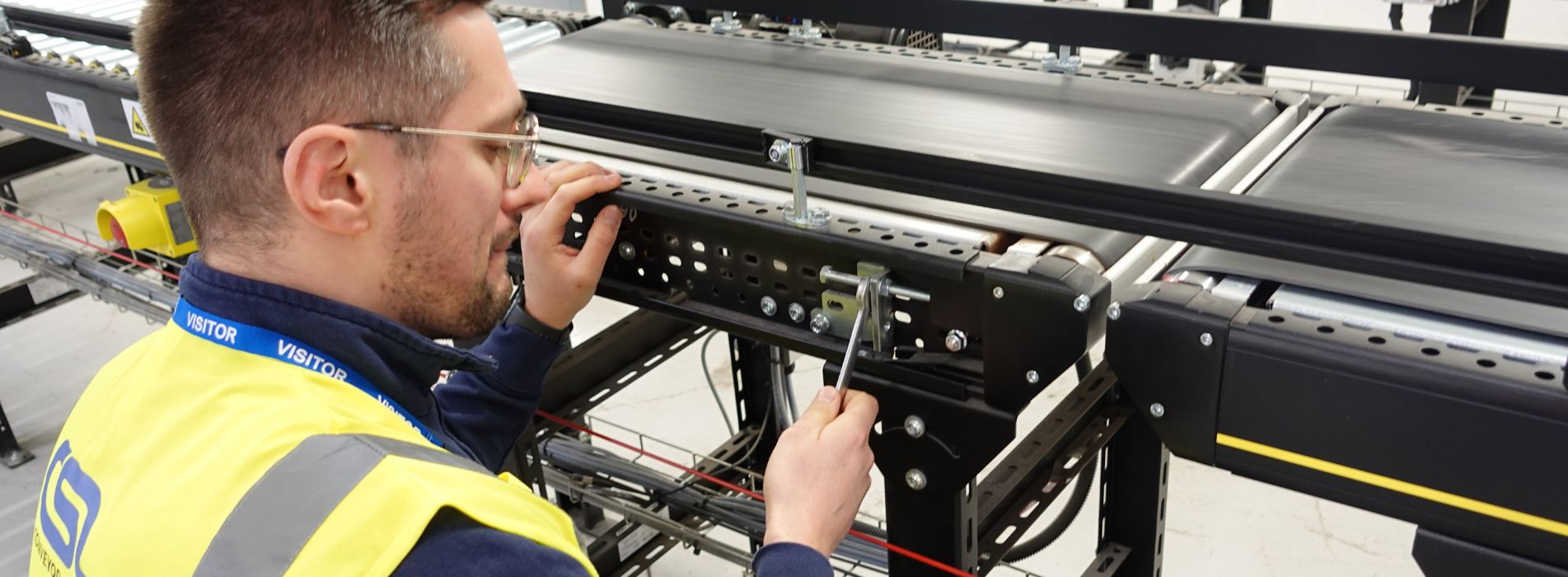
Breakdowns and repairs
With over 28 years of experience, our team is dedicated to keeping automation and conveyor systems running at peak performance. We provide expert maintenance, servicing, and support, ensuring reliability and efficiency. We deliver tailored maintenance solutions that minimise downtime and extend the lifespan of critical systems.
For more information, contact us at 01283 55 22 55.
ConveyorCare Clients






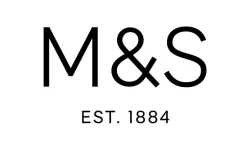








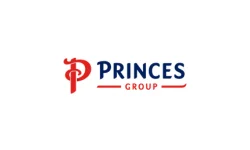



automation Breakdowns
CSL understand the importance of your conveyor and automation system, in the rare event of a breakdown we will organise one of our qualified engineers to visit site ASAP and carry out the repair.
We carry out reactive maintenance on conveyors installed by ourselves and other integrators, our engineers specialise in equipment manufactured by Conveyor Units (Uni-XU), Interroll, Logopak, Endoline, Sparck, Ambaflex, Qimarox, Intralox, but can repair almost any conveyor type/brand.

Step 1. Identifying the Issue
The first step in resolving any problem is identifying it. Common signs that something isn’t right with your automation or conveyor system include:
- Unusual noises like grinding, knocking, or vibrations.
- Visible issues such as oil leaks or wear on components.
Early identification can make all the difference, preventing minor problems from escalating into significant breakdowns. If you notice anything unusual, don’t delay—take action and get in touch with our team.
See our blog on what to look for here
Step 2. Contact Us
Your next step is simple: call or email CSL Automation. When you contact us, our experienced team will:
- Listen carefully to your concerns. Request videos and photos.
- Ask targeted questions about the issue to understand the problem better.
- Provide immediate advice and determine whether an on-site visit is necessary.
We’re committed to offering clear guidance right from the start, ensuring you feel supported throughout the process.


Step 3. On-Site Diagnosis
If the issue cannot be resolved remotely, we’ll arrange for one of our skilled engineers to visit your site. During the visit, we will:
- Conduct a thorough assessment of the reported issue.
- Inspect the system for any additional or underlying problems that could impact performance.
Our comprehensive approach ensures we address not just the immediate concern but also any potential risks, giving you peace of mind that your system is in optimal condition.
Step 4. Preparing a Quote
Once the on-site diagnosis is complete, we’ll compile the engineer’s findings into a detailed report and prepare a transparent quote for the recommended work. This quote will include:
- A clear explanation of the issue.
- A breakdown of the required repairs.
We’ll send the quote to you promptly and work with you to ensure you’re fully informed and comfortable with the proposed solution before proceeding.


Step 5. Fixing the Issue
After you approve the quote, our engineers will return to your site to perform the repair work. Here’s what you can expect during this stage:
- Safety first: We provide comprehensive Risk Assessment Method Statements (RAMS) before starting any work.
- Efficiency: Our team works swiftly to minimise downtime and disruption to your operations.
- Reliability: We ensure that your issue is resolved effectively to prevent future problems.
With our expertise, your system will be restored to full working order in no time, allowing you to focus on what matters most: running your business.
What happens if your conveyor system or belt breaks?
If your conveyor belt breaks, the immediate impact is downtime, which can cause backlogs in order fulfilment, missed deadlines, and financial losses. In some industries, such as food processing or e-commerce, even short delays can disrupt supply chains.
When a breakdown occurs, CSL can:
- Dispatch an engineer quickly to assess and repair the fault.
- Provide emergency belt replacements for worn, torn, or damaged belts.
- Offer temporary workarounds to keep some parts of your system operational while repairs are underway.
- Inspect related components to prevent follow-up failures.
If your conveyor breakdown impacts order fulfilment, our Order Packing and Order Picking systems can be reconfigured to maintain productivity during downtime.

Frequently Asked Questions
Why should I hold spare parts for my conveyor system?
Holding spare parts for your conveyor system minimises downtime and ensures continuous operation. In the event of a component failure, readily available spare parts allow for quick replacements, reducing the impact on production schedules and preventing costly delays.
How do you troubleshoot a conveyor?
Troubleshooting a conveyor involves systematic checks to identify the root cause of the fault. Our engineers typically follow this process:
- Visual inspection – Checking for belt damage, misalignment, or debris blocking the system.
- Mechanical assessment – Inspecting rollers, bearings, motors, and tension settings.
- Electrical testing – Ensuring power supplies, controls, and sensors are functioning.
- Operational testing – Running the conveyor at low speed to pinpoint unusual noises or movements.
- Preventative recommendations – Suggesting maintenance routines or upgrades to avoid future breakdowns.
For example, if a belt conveyor repair is needed due to misalignment, we can adjust tracking, replace damaged rollers, or fit a new belt to restore smooth operation.
For moving goods between operational areas after repairs, see our Product and Material Transit and Pallet Conveyors pages.
Do you offer emergency repair services for unexpected conveyor failures?
Yes, CSL Automation offers emergency repair services for unexpected conveyor failures. Our experienced team is available to diagnose and resolve issues quickly, minimizing downtime and keeping your operations running smoothly. Whether or not we originally supplied the system, we can provide expert repairs and ongoing support. Contact us at 01283 55 22 55 or [email protected] for urgent assistance.
What are the signs that indicate our conveyor system may need repairs or upgrades?
Signs indicating the need for repairs or upgrades include increased noise, decreased throughput, frequent breakdowns, excessive wear on components, and safety hazards. Our technicians can assess your system and recommend appropriate solutions.
How do you handle warranty claims and support for conveyor components and systems installed by CSL?
CSL stands behind the quality of our products and services. We handle warranty claims promptly and provide ongoing support for conveyor components and systems installed by our company, ensuring customer satisfaction and peace of mind. We only work with trusted partners for all of the equipment we install and with reputable equipment manufacturers.
What are the most common causes of conveyor downtime, and how can we prevent them?
Common causes of conveyor downtime include belt misalignment, bearing failures, material jams, and motor issues. Preventive measures such as regular maintenance, proper operator training, and installing sensors for early detection can help prevent downtime.
Types of Conveyor System Breakdowns
Electrical
Mechanical
More Information
Understanding conveyor system breakdowns
Conveyor systems are vital components of any environment where the smooth flow of products and materials is crucial. They help to improve efficiency, maximise productivity, minimise downtime, and reduce labour costs. Because of their essential role, these systems must be kept running optimally.
At CSL Automation, we understand the importance of keeping your systems operating at peak efficiency. That’s why we offer a range of services, including breakdown repair, to reduce downtime and increase productivity in your workplace.
Breakdowns
We understand the importance of your conveyor system within your warehouse, fulfilment centre, or factory. In the rare event of a conveyor system breakdown, we will arrange for one of our qualified/experienced engineers to visit your site ASAP and complete the repairs needed to get you operational again.
We can repair the conveyors we install, and those other integrators install. Our engineers specialise in equipment manufactured by Conveyor Units (Uni-XU), Interroll, Ambaflex, Qimarox, Intralox, etc.
Keep your systems running
CSL Automation can help you prioritise the long-term efficiency of your conveyor and automation system. Our dedicated team is committed to keeping your system running smoothly, reducing costly downtime and boosting productivity.
Prevent breakdowns with our tailored Conveyor Care plans, designed to keep your conveyor system operating at peak performance. We offer flexible service tiers to meet your specific needs, ensuring uninterrupted operation throughout the year.
Explore our service levels here to find the perfect fit for your system’s maintenance requirements.