
Spare Parts
With over 28 years of experience, our team is dedicated to keeping automation and conveyor systems running at peak performance. We provide expert maintenance, servicing, and support, ensuring reliability and efficiency. We deliver tailored maintenance solutions that minimise downtime and extend the lifespan of critical systems.
For more information, contact us at 01283 55 22 55.
ConveyorCare Clients






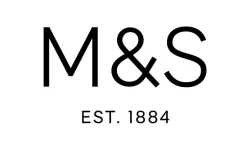








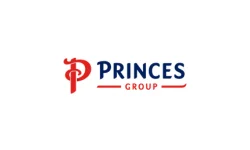



The value of minimised downtime
In the event of a conveyor system malfunction, every minute of downtime counts.
That’s why having spare parts on hand is vital. It allows for the swift commencement of repairs and minimises disruption to operations.
This prevents potential losses in productivity and revenue and helps maintain customer satisfaction by ensuring order fulfilment is quickly resumed.

Benefits of Holding Spare Parts
- Reduced costs – Repairs can often be done on the first visit
- Significantly reduced downtime and lost profits
- Improved safety – damaged parts can be promptly replaced
- Spares available from a wide range of manufacturers

spare part packages
CSL offer spare part packages to suit your needs, budget and dependency on the automation system. The ConveyorCare team will put together a spare parts list with priorities and also lead times to help you make an informed decision on which package to order.
We can supply packages such as adhoc, frontline breakdown parts, critical wear parts, Category A,B,C parts and more. These kits include mechanical, electrical and safety related parts for a comprehensive kit of spare parts.
Frequently Asked Questions
What types of spare parts should we keep on hand to minimise downtime?
It’s advisable to keep a stock of commonly replaced parts such as belts, rollers, bearings, and motor components. Our team can provide guidance on which spare parts are essential based on your specific conveyor system.
What package do you recommend for us?
Our spare part packages are based on categories:
- High Risk parts
- Medium risk
- Low Risk
These categories are determined from our experience, lead times, dependency/criticalness along with manufacturers recommendations.
Can CSL manage our spare parts for us?
More Information
The value of minimised downtime
- In the event of a conveyor system malfunction, every minute of downtime counts. That’s why having spare parts on hand is vital. It allows for the swift commencement of repairs and minimises disruption to operations. This prevents potential losses in productivity and revenue and helps maintain customer satisfaction by ensuring order fulfilment is quickly resumed.
Reduced repair costs
- Repairs requiring special parts can escalate costs in expedited delivery. The need to source and ship parts can significantly add to the repair bill. Yet, with spare parts available on-site, these costs can be reduced.
The power of enhanced efficiency
- With spare parts on-site, technicians can diagnose and resolve issues more swiftly. This efficiency reduces the overall repair time. This means your conveyor system is back to full operation faster, contributing to your warehouse productivity.
The priority of safety
- Malfunctions in conveyor or automation systems can sometimes pose safety risks. By having spare parts on-site, you can minimise risks. Quick repairs can occur to reduce the duration of potential exposure to hazardous situations for your workforce.
The assurance of reliability
- The availability of spare parts enables regular maintenance and repair. In turn, this improves the reliability of your conveyor and automation systems. This proactive approach reduces unexpected downtime, ensuring operations run smoothly and reliably.
Conveyor Systems Ltd spare parts packages
We understand the immense value of having spare parts readily available. We offer bespoke spare parts packages tailored to the needs of your warehouse conveyor and automation systems. This ensures you always have the right parts on hand;
- Facilitate swift and efficient repairs
- Maximise system reliability
- Enhance overall safety
Keeping spare parts onsite is more than a wise investment. It is a commitment to your warehouse operations’ sustained productivity, safety, and efficiency.