Interfloor Conveyor system for Ingram Micro
Ingram Micro Commerce & Lifecycle Services, Northampton DC
As the world leader in logistics, commerce enablement, and device lifecycle services, Ingram Micro Commerce & Lifecycle Services plays a pivotal role in bridging supply and demand. Through a wide spectrum of services, ranging from cross-border fulfilment, returns management, to IT asset disposition, this global entity facilitates growth, augments ROI, and safeguards clients’ interests.
Ingram Micro caters to a diverse customer base — from emerging brands to Global 2000 enterprises — fueling their success through an expansive warehousing network, cutting-edge technology, strategic alliances, and decades of industry experience.
The Challenge: Streamlining Operations in Daventry
For its Daventry operation, Ingram Micro sought a system that would seamlessly integrate the packing and dispatch process while optimising space with a new three-tier mezzanine. The challenge was to manage boxes, cartons, and poly bags from all three levels, consolidating them on the ground floor before dispatch.
This ground-floor operation would function independently, utilising standalone conveyors. Furthermore, the system needed to be reversible to accommodate replenishment and alternative operations, requiring each line to have three distinct operating functions.
Multipurpose System: Three Modes for Maximum Efficiency
In line with Ingram Micro’s requirements, the system operated in three modes: decline to dispatch, reverse incline for stock replenishment, and a back-up mode for clearing the line into wheeled magnums during system issues.
Reflecting on the project, a spokesperson from Ingram Micro praised the new system for meeting their requirements, predicting that the benefits—increased throughput and reduced operating costs—would soon materialise.
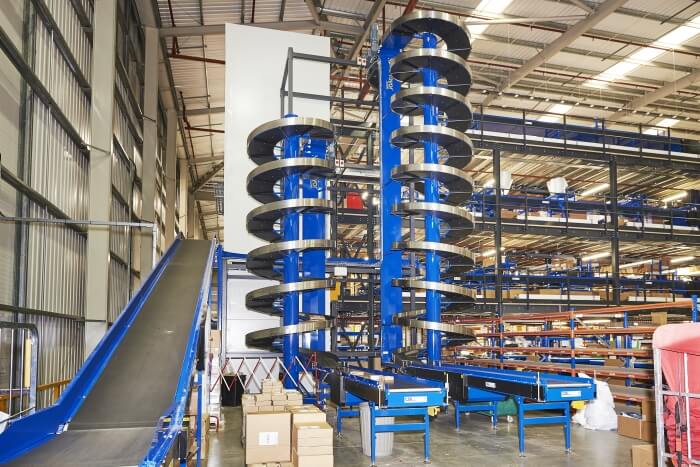