
ConveyorCare from CSL
With over 28 years of experience, our team is dedicated to keeping automation and conveyor systems running at peak performance. We provide expert maintenance, servicing, and support, ensuring reliability and efficiency. We deliver tailored maintenance solutions that minimise downtime and extend the lifespan of critical systems.
For more information, contact us at 01283 55 22 55.
ConveyorCare Clients






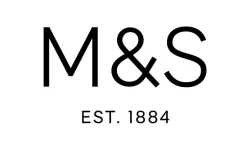








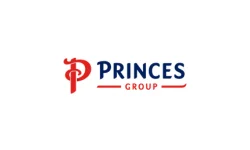



ConveyorCare from CSL
CSL Automation will be your dedicated partner in conveyor system maintenance. We understand the pivotal role that your conveyor system plays in your day-to-day operations.
ConveyorCare from CSL is a comprehensive suite of maintenance and servicing solutions designed to cater to the unique needs of your specific conveyor system.
ConveyorCare is designed to minimise downtime, reduce operational costs, and address safety concerns to ensure that your conveyor system operates at peak performance.

Why Choose CSL for Your Conveyor Maintenance?
Regardless of who initially installed your conveyor system, we can offer a care package that keeps it up and running. You can choose from three distinct tiers of service â Bronze, Silver, and Gold â each offering a comprehensive set of features and benefits.


more information
Proactive Conveyor Servicing & Maintenance
Regardless of who initially installed your conveyor system, we can offer a care package that keeps it up and running. You can choose from three distinct tiers of service â Bronze, Silver, and Gold â each offering a comprehensive set of features and benefits.
Bronze tier: Our bronze tier provides a solid foundation for conveyor system maintenance. It includes a personalised service and maintenance plan to address your systemâs specific needs and usage level.Â
Silver tier: Our silver tier strongly emphasises Preventative Planned Maintenance (PPM) by including electrical/safety circuit inspections. We proactively identify and address potential mechanical faults before they escalate, ensuring your entire conveyor systemâs smooth and cost-effective operation.Â
Gold tier: Our gold tier offers the pinnacle of conveyor system care. In addition to a tailored service and maintenance plan and the benefits of PPM, youâll also enjoy a generous 10% discount on spare parts packages, further optimising your maintenance budget.
Emphasis on preventative planned maintenance (PPM)
Our maintenance philosophy revolves around Preventative Planned Maintenance (PPM), simplifying the complex task of keeping your conveyor system in top shape. By spotting and addressing potential issues before they become critical, we guarantee that your conveyor system consistently runs at its optimal performance level.Â
No matter which service tier you choose, a mechanical service contract is included, providing comprehensive mechanical checks and necessary repairs.
Why Choose CSL for Your Conveyor Maintenance?
When you choose âConveyor Care from CSL,â youâre making a strategic investment in the longevity and efficiency of your conveyor system.Â
Our team is passionate about ensuring your systems operate seamlessly, minimising costly interruptions, and enhancing overall operational performance. Trust CSL as your dedicated partner in achieving conveyor system excellence.
Let us help you keep your operations running smoothly while minimising operational costs and enhancing overall efficiency.
- Contact us for a consultation: Our experts will discuss your conveyor system needs and requirements.
- Request a quote:Â You can obtain a detailed quote based on your chosen tier of âConveyor Care from CSL.â
- Explore our service tiers: Learn more about the Bronze, Silver, and Gold service tiers to find the best match for your conveyor systemâs maintenance needs.
Modernisation & Upgrades
As your business grows, we can adapt your system layouts to help you cope with changing scopes, evolving products, shifts in company direction, or increased throughput demands.
Our team excels in implementing changes that can help your business grow, including:
- Reconfigurations
- Upgrades
- Extensions
- Relocations
- Fire escape route changes
- Changes in routes/scope or function
- Safety system upgrades
- Improvements in energy efficiency
- Control and software changes
Our continuous improvement programs are tailored to optimise workflow while reducing operational costs. We understand the critical nature of your conveyor system and will define a detailed implementation plan, minimising downtime and operational disruption. Beyond cost savings, these changes also reduce environmental wastage.