
Electrical Servicing
With over 28 years of experience, our team is dedicated to keeping automation and conveyor systems running at peak performance. We provide expert maintenance, servicing, and support, ensuring reliability and efficiency. We deliver tailored maintenance solutions that minimise downtime and extend the lifespan of critical systems.
For more information, contact us at 01283 55 22 55.
ConveyorCare Clients






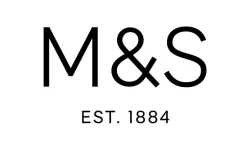








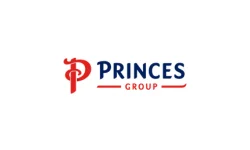



Electrical Servicing
Conveyor and automation systems are complex. They rely on mechanical parts and electrical systems, too. These systems are crucial for operation. Regular Planned Preventative Maintenance (PPM) enhances performance and ensures safety.
Electrical faults can disrupt operations and pose safety risks. By identifying and rectifying risks, damaged or worn parts before they fail boost reliability and reduce the chances of unexpected, costly failures.


Electrical Safety
The CSL ConveyorCare electrical service contract includes inspecting components such as:
- eStops
- Safety circuits
- Breakers
- Wiring
- Field devices
Frequently Asked Questions
Why is conveyor safety important?
Issues with conveyor systems can cause more prominent problems later on if not tended to immediately. This can be both costly and harmful to employees. By ensuring your conveyor system is regularly maintained, you can have peace of mind knowing any issues will be flagged immediately mitigating any serious problems in the future.
How do you identify electrical hazards?
Different conveyor systems come with unique electrical hazards. In belt conveyors, the motor can cause issues if not properly maintained. Overheating motors can lead to electrical failures and even fires. Roller conveyors, on the other hand, depend on sensor systems. Faulty sensors can cause products to collide or pile-up together, leading to increased wear and potential equipment damage.
What should I expect from an electrical service?
What does an electrical service involve? It includes inspecting and testing all electrical parts. These parts include motors, sensors, and control systems. Any worn or damaged parts will be replaced. System updates are also performed to enhance efficiency and safety.
At CSL Automation, we understand the importance of the electrical safety of your systems. Our Conveyor Care contracts offer tailored maintenance solutions. With the tiered packages there’s an option for every requirement and budget. By choosing CSL, you ensure your conveyor system gets the best care.
More Information
Electrical Servicing
Conveyor systems are complex. They don’t just rely on mechanical parts, but electrical systems too. These systems are crucial for operation. Regular Preventative Planned Maintenance (PPM) enhances performance and ensures safety.
Electrical faults can disrupt operations and pose safety risks. For instance, a short circuit might start a fire. This could endanger personnel and infrastructure. Further, malfunctions in electrical components could damage the mechanical parts. The result? Costly downtime and repairs.
So what can you do to prevent any issues with your conveyor systems?
Regular maintenance: A key to safe operations
Regular electrical maintenance is essential. It makes sure your conveyor system operates safely and efficiently. The process helps identify and fix potential issues before they escalate. This proactive approach boosts reliability and reduces the chances of unexpected failures. Above all, it ensures employee safety.
At Conveyor Systems, we offer maintenance services in all aspects of conveyor systems including electrical and mechanical servicing, breakdowns and spare parts. We aim to ensure our customer’s conveyor systems are working as efficiently as the day they got them.