Automotive Automation with CSL
A leading UK supply chain management company specializing in automotive parts distribution awarded Conveyor Systems Ltd (CSL) a contract to design a conveying solution for its Distribution Centre, aiming to improve inbound and outbound stock replenishment and order picking efficiency.
CSL replaced an existing pallet goods lift with two spiral elevators, enhancing the flow of goods between the ground floor and mezzanine level. This system eliminates the need for palletising or depalletising tote bins, reducing manual handling and improving order picking accuracy. Inbound goods are placed on powered roller conveyors and fed via spiral elevators to the mezzanine for stock replenishment.
For order picking, parts are transported to the ground floor using another spiral conveyor, where they are consolidated and prepared for despatch. The reversible spiral conveyors offer flexibility, enabling uninterrupted operations during maintenance.
The system is designed for energy efficiency, with features such as remote stop/start buttons and sleep timers to reduce energy consumption and prolong component life. The customer has already seen improved speed and handling capacity and plans to expand the system to other warehouses.
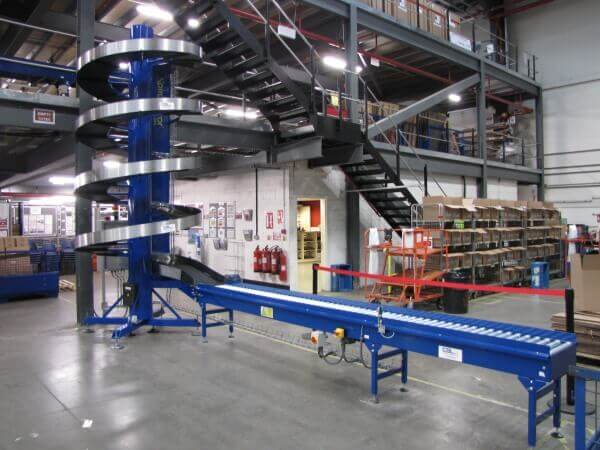