Automated Replenishment Systems
With a greater demand for products than ever before, warehouses and distribution centres can find it hard to keep up. Especially for businesses that manually input stock levels, it can be difficult to track products accurately, which can result in under and over-stocking of items. This can have a knock-on effect of losses in sales and excess costs.
A solution to this is automated replenishment systems. Automated stock replenishment is a combination of technology and software used to keep track of stock levels. By integrating elements such as a Warehouse Management System (WMS), sensors and even robots, you can effectively manage your stock levels without the extra hassle of manually inputting numbers.
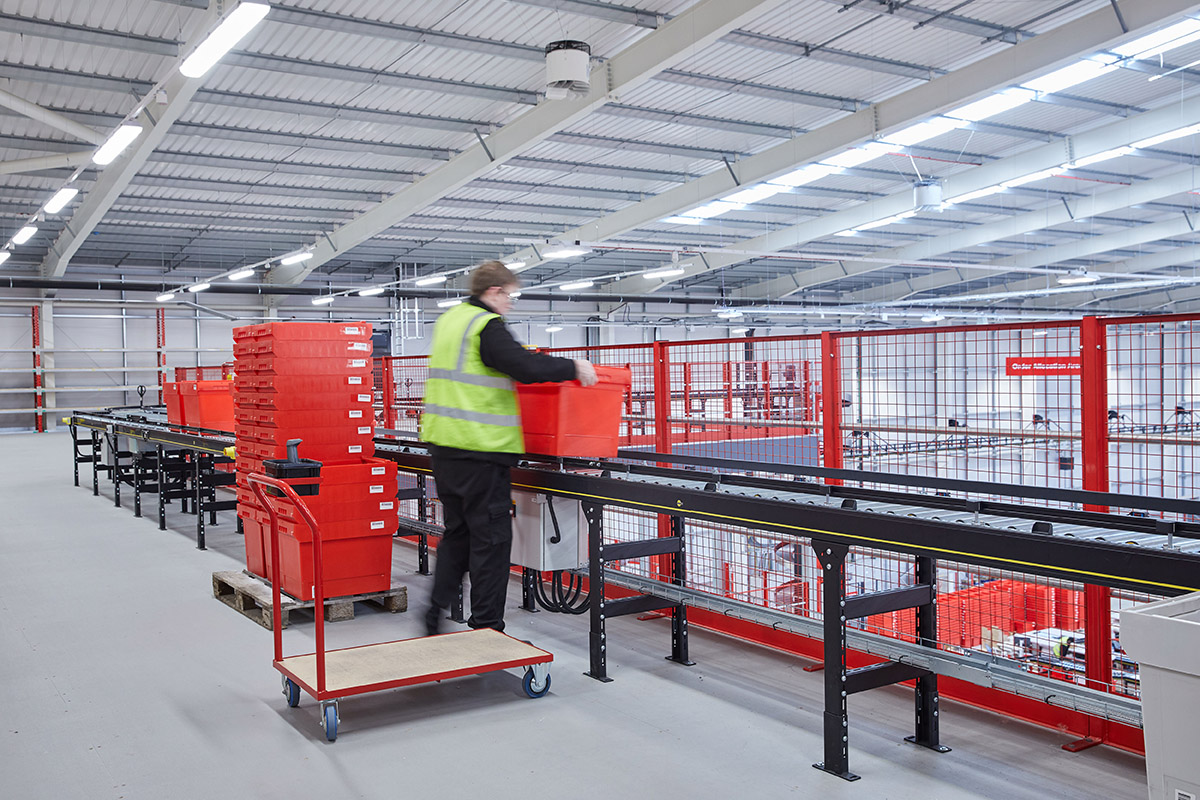
Transform Stock Replenishment with Automation
Efficient stock replenishment is essential to maintaining uninterrupted operations and meeting customer demand. By utilising conveyor systems and automation technologies, businesses can streamline the replenishment process, enhance inventory management, and maximize operational efficiency across diverse industries.
Challenges in Stock Replenishment
Traditional stock replenishment comes with a multitude of challenges, including:
- The need for timely replenishment to prevent stockouts
- Efficient utilisation of warehouse space
- Accurate inventory management
In addition to this, the manual replenishment process also has a number of caveats as it is often labour-intensive, prone to error and may result in inefficiencies that impact overall productivity and customer satisfaction.
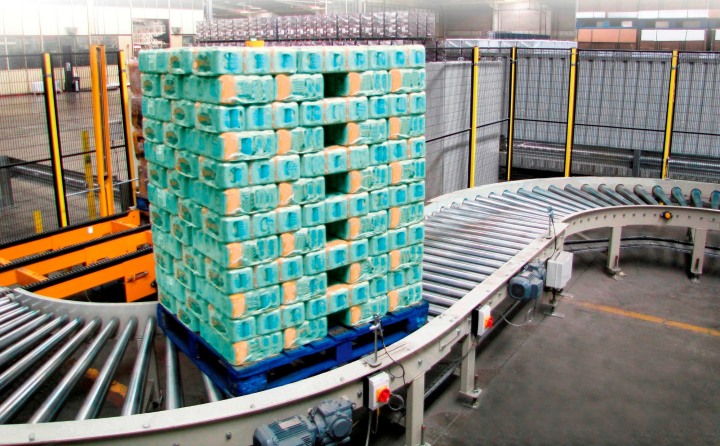
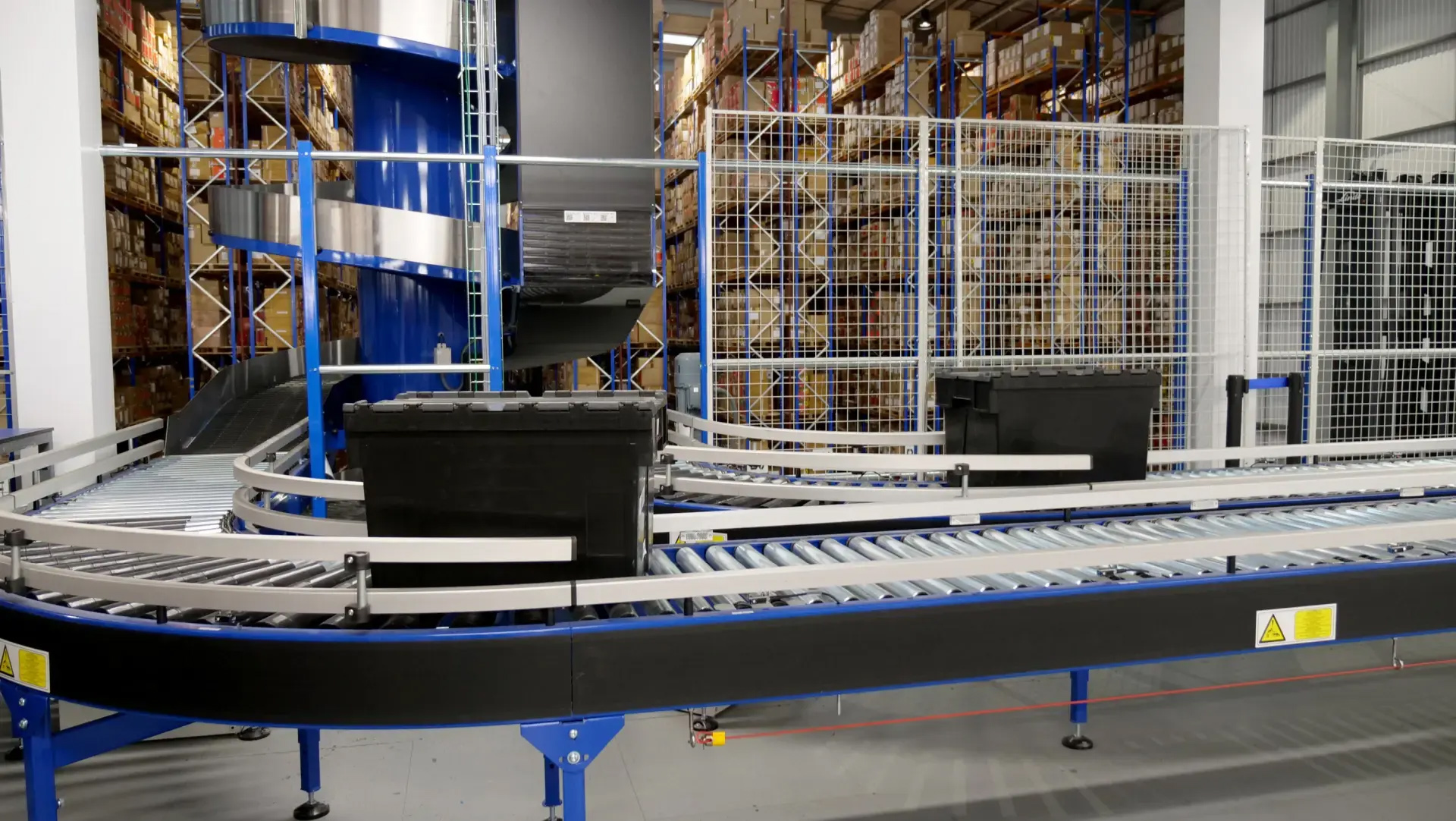
Benefits of Automated Stock Replenishment
Continuous flow of goods: Conveyor systems facilitate the seamless movement of goods from receiving areas to storage locations, ensuring a constant flow of inventory within the warehouse or facility. Automated conveyance eliminates bottlenecks and delays associated with manual transport, enabling timely replenishment to meet fluctuating demand.
Dynamic replenishment algorithms: Integration with inventory management systems enables the implementation of dynamic replenishment algorithms that optimise stock levels based on demand forecasts, sales data, and lead times. Automated replenishment triggers ensure that stock is replenished proactively, minimising the risk of stockouts and maximising product availability.
Efficient space utilisation: Conveyor systems optimise the utilisation of warehouse space by facilitating vertical and horizontal movement of goods to and from different mezzanine floors via spiral conveyors for example. Automated storage and retrieval systems (AS/RS) enable high-density storage, allowing businesses to maximise storage capacity and reduce storage costs while maintaining accessibility to the inventory for replenishment purposes.
Reduced labour costs: Automation of replenishment tasks reduces reliance on manual labour, freeing up personnel to focus on value-added activities such as quality control, order fulfilment, and process optimisation. Reassigning employees to less labour-intensive roles also reduces the risk of injury. By automating repetitive tasks, businesses can minimise labour costs, improve productivity, and enhance overall operational efficiency.
Real-time visibility and control: Integration with Warehouse Management Systems (WMS) provides real-time visibility into inventory levels, replenishment status, and workflow performance. Automated monitoring and reporting enable proactive decision-making, allowing businesses to respond swiftly to changes in demand and optimise replenishment strategies accordingly.
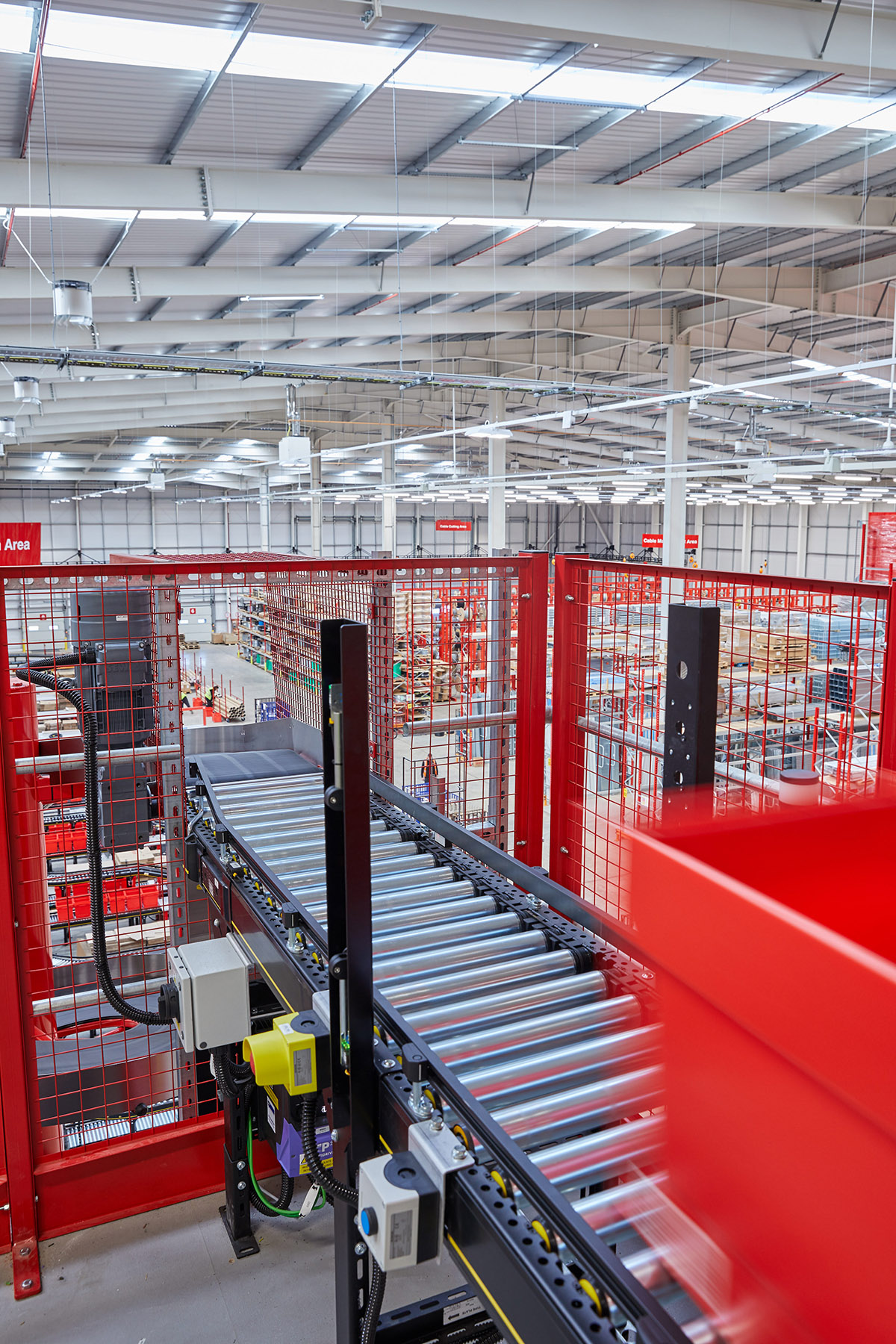
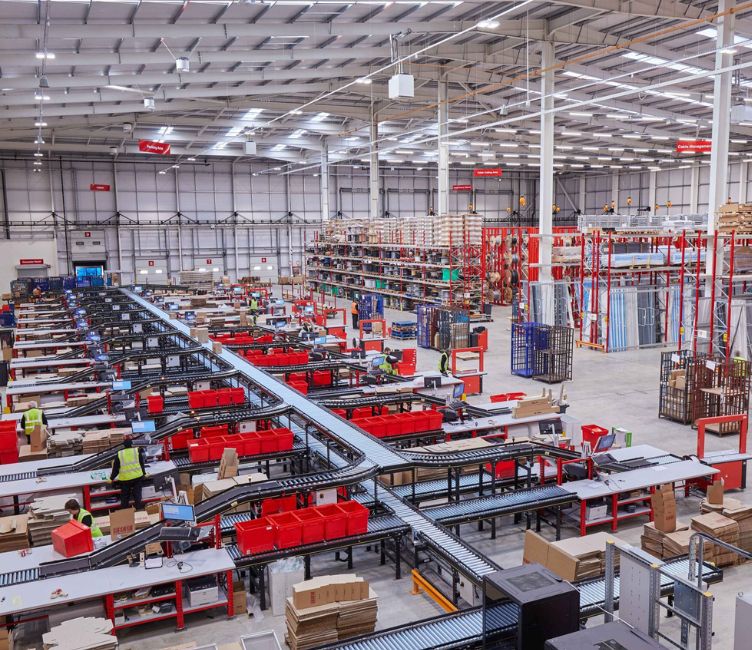
Technology To Elevate Your Warehouse Replenishment Process
An automated replenishment system consists of a number of elements that can vary depending on the level of automation you require. Here are just a few of the technologies used in replenishment automation:
Warehouse Management Systems (WMS)
This software oversees everything that happens in a warehouse. One key role a WMS plays in warehouse replenishment is managing inventory movement, tracking stock levels, and generating replenishment orders based on your business’s requirements.
Demand Forecasting and Predictive Analytics
Demand forecasting and predictive analytics, using advanced software and machine learning algorithms, can help your business order the optimum amount of stock. By analysing historical sales data and marketing trends, an accurate prediction of stock can be made, optimising your warehouse replenishment process.
Barcode and RFID (Radio-Frequency Identification)
Barcodes and RFID can be used to help track items and their movements around a facility and increase real-time visibility. This supports other elements of the warehouse replenishment process, such as real-time inventory control and precise stock levels.
Automated Guided Vehicles (AGVs) and Robotics
With the creation of an automated replenishment plan, technology can be used to carry out automatic replenishment. For example, AGVs and robots can be implemented to automate the picking, packing and replenishment of items. As AGVs and robots are autonomous, they are able to complete these tasks without supervision, allowing staff to focus on more skill-based tasks.
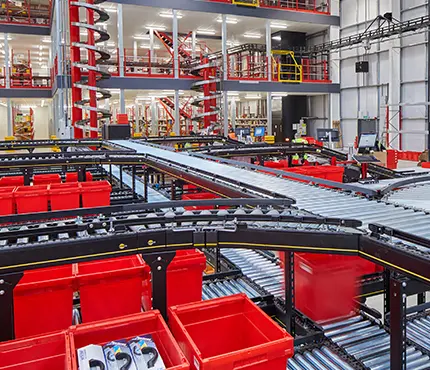
Automated Replenishment System FAQs
How can you automate the replenishment of stock levels?
By integrating Warehouse Management Systems, Demand Forecasting and Automated Guided Vehicles and Robots, you can experience an automated replenishment system. Warehouse Management Systems can allow you to oversee all the operations of your warehouse, helping you track stock levels in real time.
Additionally, Demand Forecasting provides insight into the behaviours of your customers, assisting you to only order the required amount of stock. With Automated Guided Vehicles and Robots, these processes can all be automated. From picking to packing and replenishment, these technologies can be utilised to complete more mundane tasks, allowing employees to be assigned to more skill-based tasks.
What are the benefits of automated stock replenishment?
Automating your warehouse replenishment process can bring about numerous benefits, including:
- Real-time inventory control
- Precise stock levels
- Reduced storage costs
- Waste reduction
- Effective communication throughout the whole supply chain
What is the difference between manual and automated inventory systems?
Manual replenishment systems are perfect for small businesses that have a small amount of inventory so they are able to manage their stock levels with ease without the need for automation. With larger companies, an automated replenishment system is easier as it allows for visibility of precise stock levels and forecasting, among other benefits, that can optimise a warehouse replenishment process.
Choose Conveyor Systems To Upgrade Your Stock Replenishment
At Conveyor Systems, we want to make your business processes easier, one step at a time. By implementing automated supply replenishment systems, you will no longer have to worry about manual stock tracking, which can lead to human error, and you will experience a stress-free warehouse replenishment process.
Get in touch with our experts today to take advantage of real-time inventory control, reduced storage costs and a streamlined replenishment process. Upgrade the way your replenishment system works with automated replenishment today!