New National Distribution Centre for SLS
Scientific Laboratory Supplies (SLS) began operating in 1991 and has grown to become the UK’s largest independent supplier of laboratory equipment, chemicals and consumables.
After a period of growth and positive forecasting SLS identified that the current site in Nottingham was becoming outgrown and a move to a new and much larger facility seemed the clear next step in the company’s success strategy. SLS identified a suitable site on a new commercial development on the outskirts of Nottingham, the brand-new building offered over 55,000 sq ft of space ready to be fitted out with a mezzanine, racking, shelving and a multi floor conveyor & automation system. The fit-out plans would allow SLS to process 300% more order capacity than the previous site.
Download this Case Study
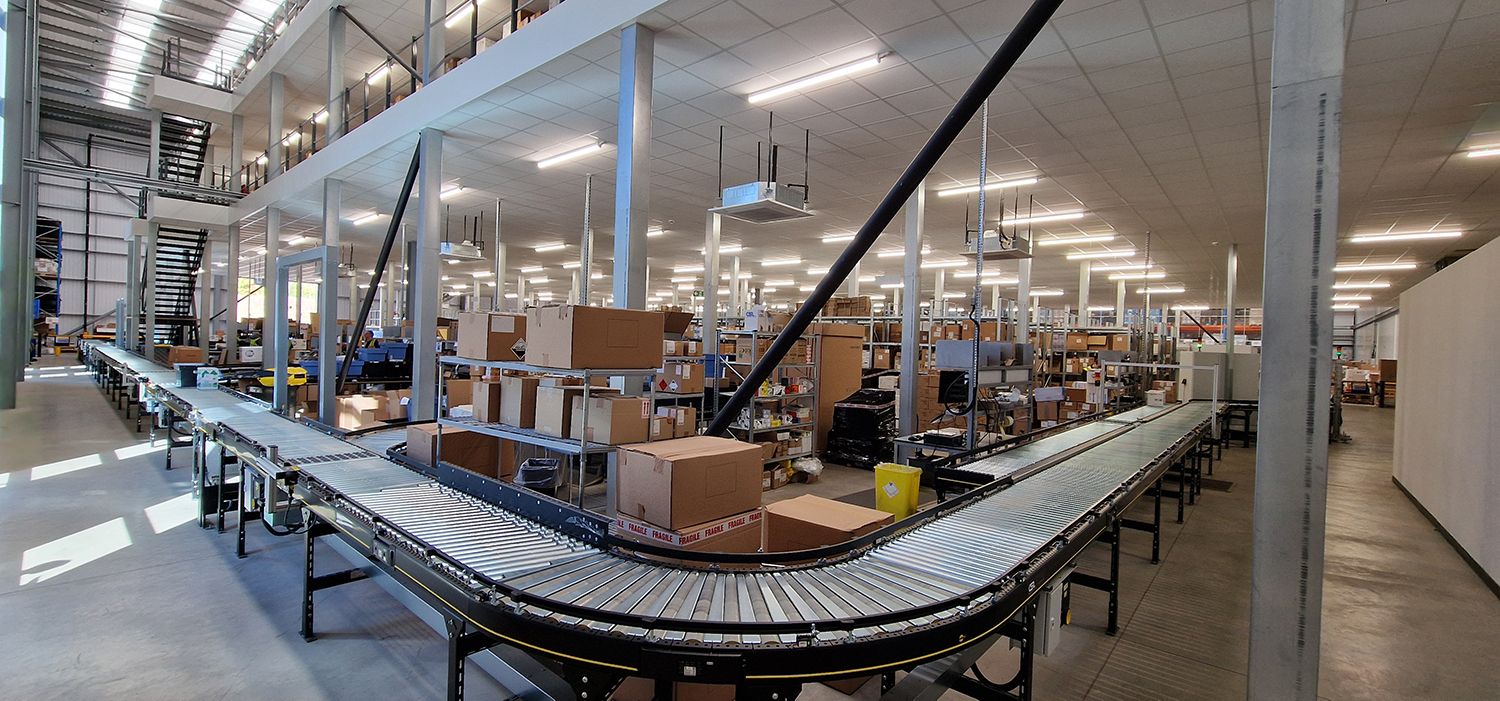
This expansion follows a significant period of growth that has positioned SLS as the UK & Ireland’s leading independent distributor of laboratory equipment. The new NDC, which is twice the size of the previous facility will enable SLS to better serve its customers by meeting demands more efficiently and enhancing its industry-leading customer service standards. SLS wanted to maximise the warehouse capacity and to add a replenishment function alongside a full case and tote picking section. CSL demonstrated a clear outline of the solution from the outset, working closely with SLS throughout the tender process was one of the key reasons that SLS decided to partner with CSL Automation.
CSL designed the total turnkey solution focused on SLS’s current challenges & future plans and worked ways to overcome and achieve from both day one but also allow SLS to grow and expand into the proposed solution. The CSL solutions team visited the old site multiple times to gain this understanding along with discussions with Operations Director, Bruce Mowbray and the team. The project ran smoothly and on schedule, as principal contractor CSL were able to organise every element of the installation including, the mezzanine, storage, automation and conveyor equipment. By being included in the project from an early stage the CSL technical team were able to work with the building contractor to include re-enforcements in the flooring to correctly support the mezzanine along with its intended loads.
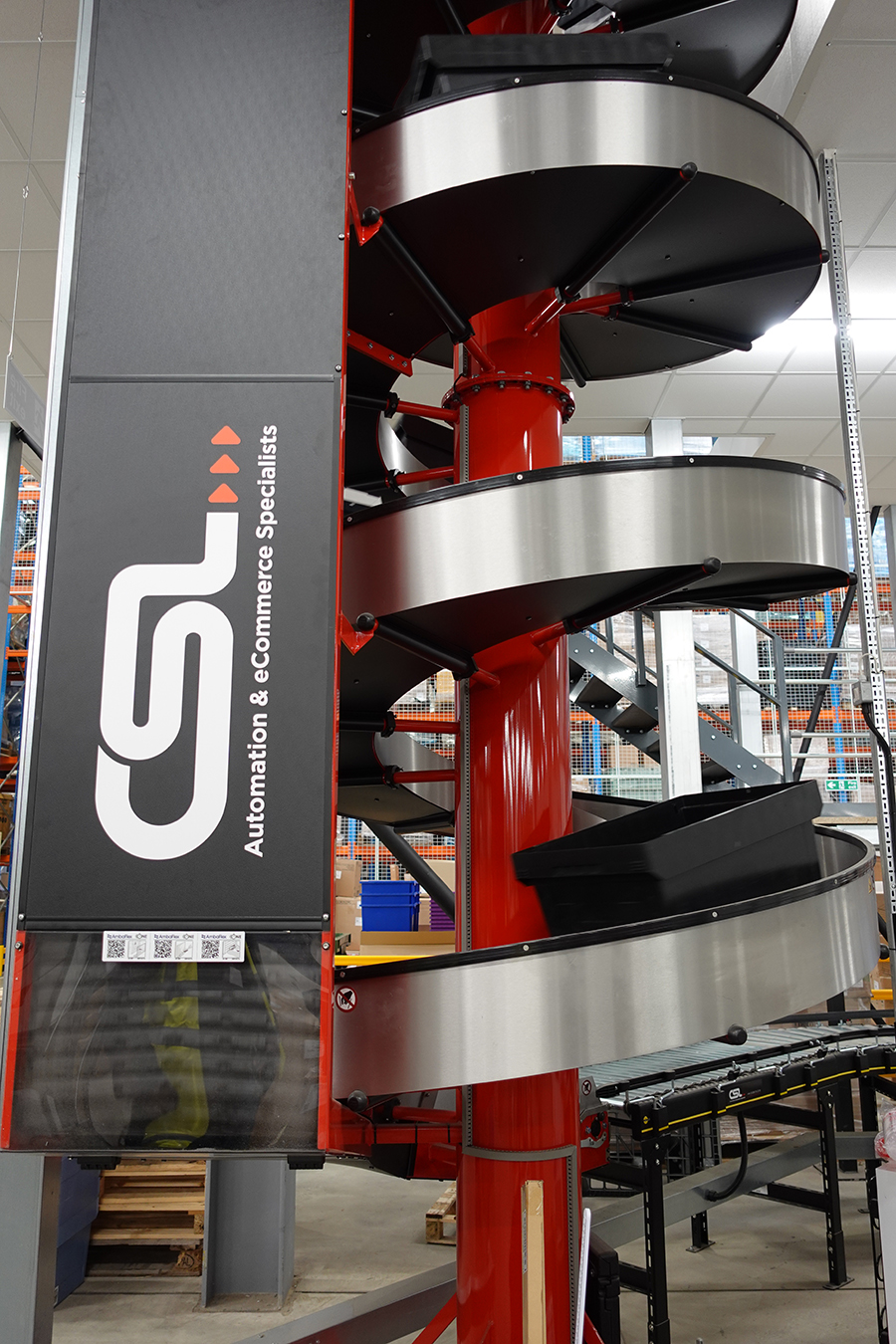
Creating relationships that last
We are proud to have completed installations for many major organisations, forging strong relationships and continuing to provide automation solutions through ongoing maintenance or follow-on projects due to expansion and our customers’ trust in CSL to meet and exceed their needs.