Conveyor systems are used all around us in different industries for a number of functions. There are conveyors everywhere from airports to supermarkets. In this blog, we delve into the intricacies of conveyor systems, from their core functionality to their applications across different industries. Conveyor systems play a pivotal role in streamlining processes in warehouses, distribution centres, and processing lines, so how can conveyor systems be used, and where can you commonly find them?
- What is a Conveyor?
- How a Conveyor System Works
- Types of Conveyor Systems
- Benefits of a Conveyor System
- Common Industries Conveyor Systems are Applied To
- Upgrade Your Warehouse With a Conveyor
What is a Conveyor?
Generally, everyone has an image in their minds when they think of a conveyor. The most common type that comes to mind is probably conveyor belts. This is because they are used in a wide variety of industries, from the baggage claim in the airport to checkouts in supermarkets, there are conveyor belts all around us. Yet, you may be wondering what a conveyor system is and how it works, so let’s delve into it.
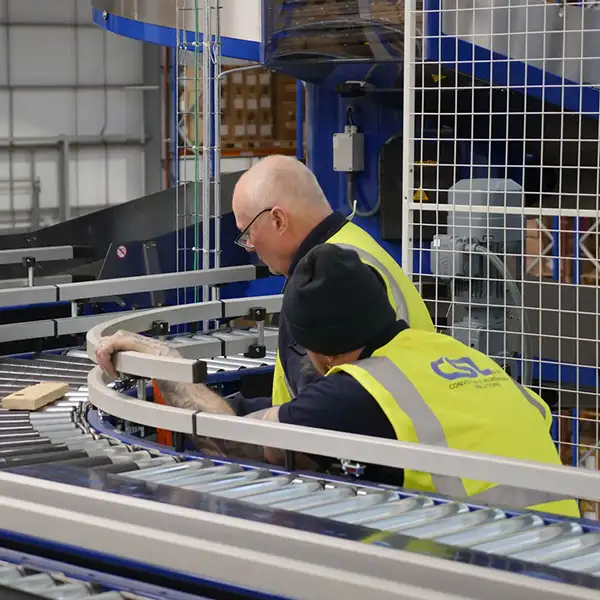
The Components of a Conveyor System
There are four main elements of a conveyor system, with each component playing a vital role in ensuring the conveyor system functions. The key components are the belt, the belt support, the pulley, and the drive unit.
The Belt
The belt is the main component you can see when looking at a conveyor belt system. The primary function of the belt is to transport the products or materials from one place to another. The belt itself can be made of various different materials depending on the situation. This includes nylon, polyester, rubber, stainless steel, and thermoplastics.
The Belt Support
The main role of the belt support is to ensure the belt itself does not sag or become misaligned. This ensures the conveyor belt is maintained over time. Heavier loads can also be transported with ease without damaging the belt in the long run.
The Pulley
The pulley plays a crucial role in the movement of the conveyor belt. Drive pulleys are connected to the motor, which transmits motion to the conveyor belt. This causes the belt to move allowing for the transport of materials. This means the direction of the conveyor system can also be controlled. Idler or redirect pulleys guide the belt in whichever direction you prefer.
The Drive Unit
The drive unit is comprised of an electric motor, gearbox, and other drive components. Connected to the pulley, the drive unit powers the movement of the conveyor belt. This enables products and materials to be transported.
Roller Conveyor Systems
Roller conveyor systems have a slightly different composition. Instead of a belt, a set of rollers are used to transport products. These rollers are cylindrical tubes or wheels placed parallel to each other along the length of a conveyor.
Additionally, roller conveyor systems can be powered by either gravity or some form of propulsion. In a gravity roller conveyor, items are moved along using the force of gravity. In motorised systems, a motor is used to drive the rollers to transport items.
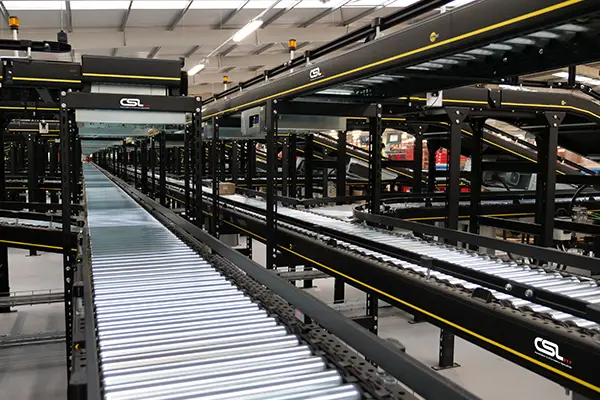
How a Conveyor System Works
By combining all these components, a conveyor system is created. Each component works together to transport items. The conveyor belt (or rollers) is placed along the length of the conveyor system to provide the area of transportation. Conveyor belts are stretched into a closed loop across the pulleys. The drive unit then powers the pulleys to transmit motion to the conveyor belt.
In situations where turns or bends are needed in the conveyor system, cone-shaped rollers/wheels are used. This is in place of a conveyor belt, as a belt would be unable to bend without becoming twisted.
Types of Conveyor Systems
There are various types of conveyor systems that are applicable to different industries depending on the required function. Below, we have compiled a list of the most common types of conveyor systems and their uses to help you find the right conveyor system for you.
Belts Conveyor System
This conveyor system utilised conveyor belts to transport items. Made of a range of materials, including nylon, rubber, or stainless steel, this form of conveyor has many applications. From manufacturing to pharmaceuticals, conveyor belts are very versatile.
Roller Conveyor System
Roller conveyors are typically used for larger items due to the placement of the rollers. There are different types of roller conveyor systems: gravity or powered. The functionality of this conveyor system depends on which form of roller conveyor system is utilised. Generally, roller conveyor systems have more benefits than belt conveyor systems as features like sortation can be implemented using this system. However, the extent of the benefits would depend on the needs of the client.
Slat Conveyor System
Slat conveyors are similar to conveyor belts but instead of a conveyor belt, a slat and chain system is used. The slats are made from steel panels that are attached by a chain allowing for movement. This form of conveyor system is commonly used in production and assembly lines.
Vertical Conveyors
Another form of conveyor system is a vertical conveyor. These conveyors work to transport items vertically rather than horizontally like standard conveyor systems. There are many different forms of vertical conveyor systems including spiral conveyors, mezzanine lifts, and screw conveyors. Each with their own features, vertical conveyors are an excellent solution for smaller facilities that want to make the most of their space.
Spiral Conveyors
Spiral conveyor systems are a form of vertical conveyor, used to transport items from one level to another. This can be either upwards or downwards depending on the type of spiral conveyor. There are both powered and non-powered (gravity) spiral conveyors each with a different function.
Powered systems are commonly used to transport items upwards to other levels of a facility whereas gravity conveyors are used to transport items downwards. This system is perfect for warehouses where there is a limited amount of space.
Benefits of a Conveyor System
There are several benefits of a conveyor system that can enhance the way your facility operates including:
- Ability to move heavy objects – by utilising machinery rather than humans to move heavy objects, you can improve the rate at which the items are transported
- Less physical strain – employees will have less physical strain moving objects manually enabling a safer working environment
- Capable of moving various items – conveyor systems are versatile meaning they can transport a wide range of items at a high quantity
- Potential to move items to elevated heights – vertical conveyor systems are able to transport items from one level to another
- Increased efficiency and productivity – conveyor systems allow for a constant flow of materials enabling a consistent production pace and removing bottlenecks
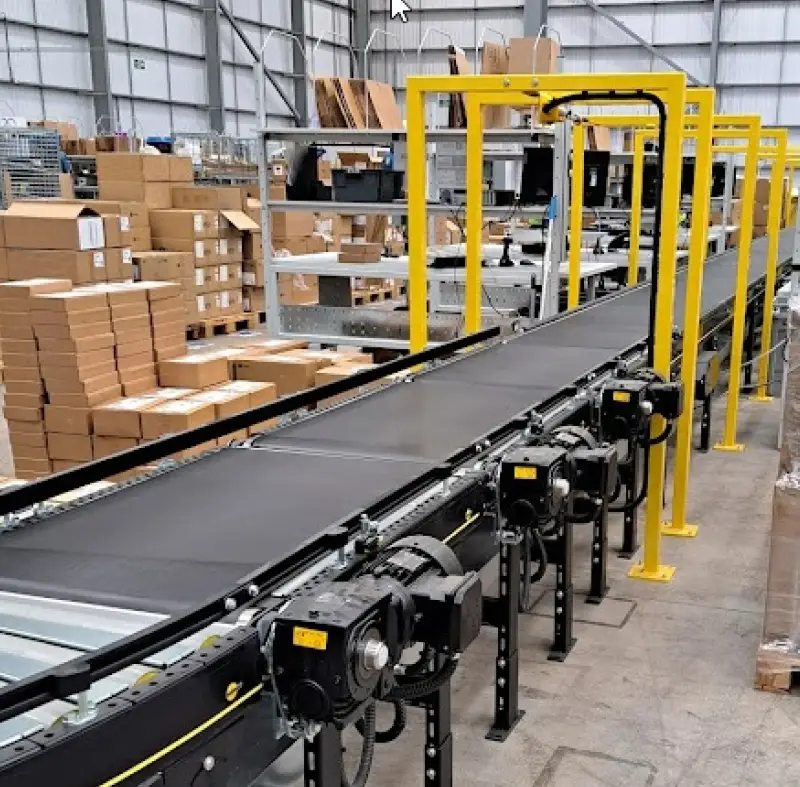
Common Industries Conveyor Systems are Applied To
With the versatility of conveyor systems, many industries can benefit from implementing conveyors to increase efficiency. There are various factors that need to be considered when applying conveyors to different industries.
Type
The type of conveyor system can be applied to various industries. For instance, spiral conveyors can be used in warehousing and distribution as the need to transport items vertically may be more critical for this industry based on warehouse space. Roller conveyor systems, on the other hand, may be more beneficial for pallet and carton handling in distribution centres and manufacturing as this form of conveyor is able to carry heavier loads.
Material
The material conveyor systems are made of can also change the application of conveyor systems. For example, conveyor belts made of stainless steel can be utilised in the food and pharmaceutical industries as stainless steel is a food-grade material. Whereas, conveyor belts made of thermoplastics or rubber can be applied to chemical manufacturers as these materials may be able to withstand high temperatures and corrosive.
Design
The design of conveyor systems can also be tailored to certain industries. Taking into account how easy the conveyor is to clean may be a factor in the design when implementing a conveyor system in a food factory. Additionally, if automatic sorting is a function of a facility, then ensuring gaps are maintained between products will be important so that the barcodes of the items can be scanned.
If you need advice on what type of conveyor system is perfect for your facility, contact us and one of our experts will be ready to start enhancing your facility today.
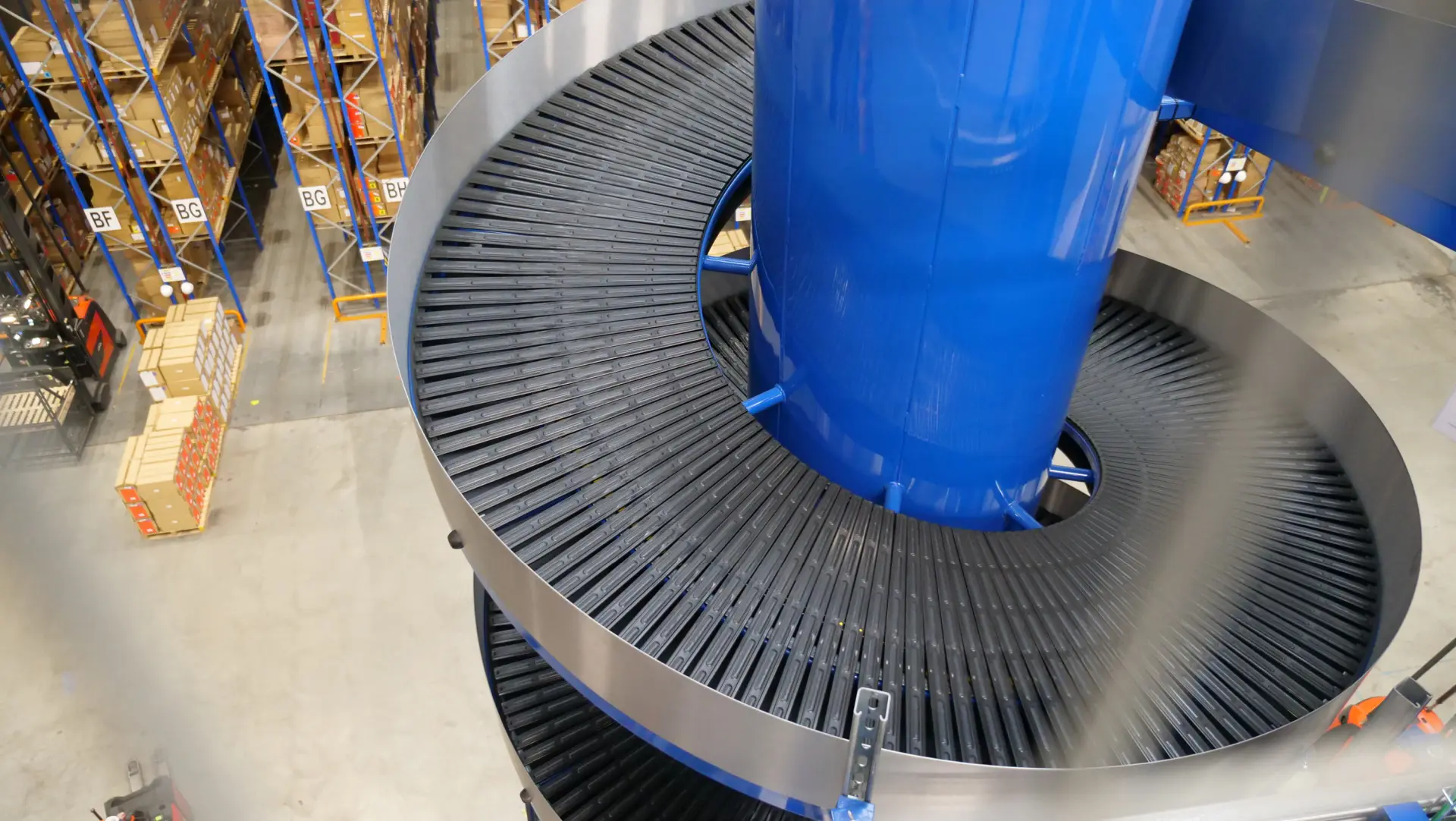
Upgrade Your Warehouse With a Conveyor
At Conveyor Systems, we pride ourselves in helping our clients get the most out of their facilities. With a wide range of applications to many different industries, a conveyor system can be applied to your facility to enable your business to be more efficient and productive. From less strain for your employees to increasing usable space in your facility, conveyors could be the solution you are looking for to elevate your business. Contact us today to take your facility to the next level.
Conveyor System FAQs
What are conveyor systems commonly used for?
The primary function of a conveyor system is to transport items from one location to another. Whether that be from one area to another or from one level or another, conveyor systems can be versatile in their function.
What is an example of a conveyor system?
There are many different conveyor systems that you can see in your everyday life. For example, escalators, conveyor belts at supermarket checkouts, baggage claim at the airport, and ski lifts. This shows the versatility of conveyor systems as they have many different applications in various different industries.
Are conveyor belts used in factories?
Conveyor belts are very applicable to factories as they can easily transport items from one area to another. This can be in different industries such as food and beverages or chemical processing depending on the materials used to make the conveyor belts.